Fabrication of porous geopolymers utilizing aluminum wastes as foaming agent
DOI:
https://doi.org/10.55713/jmmm.v34i2.1966Keywords:
Aluminium, Geopolymer, porous materialsAbstract
Porous geopolymers (PG) are attractive due to their simple fabrication and diverse applications. This work presents a method for fabricating PG by using aluminum salt slag (ASS) as a foaming agent and metakaolin (MK) as the precursor. Sodium silicate (Na2SiO3) and sodium hydroxide (NaOH) are used as alkali activator solutions. The results show that the PG is fabricated by using the sequence mixing method. ASS was milled to a size of 4 µm, then mixed with an NaOH solution for 30 min. After that, MK and Na2SiO3 solution were added. The weight ratio of Na2SiO3/NaOH and solid/liquid was 2.0 and 0.6, respectively. The 7-day cured PG with 5 wt% ASS achieves a strength of 15 MPa, which is close to the minimum requirement of Portland cement of 19 MPa. PG strength decreases, while setting time and pore size increase with increasing ASS content. The knowledge of this work enables the utilization of ASS as a valuable geopolymer foaming agent.
Downloads
References
L. Grande, M. Á. Vicente, S. A. Korili, and A. Gil, “Synthesis strategies of alumina from aluminum saline slags,” Process Safety and Environmental Protection, vol 172, pp. 1010-1028, 2023. DOI: https://doi.org/10.1016/j.psep.2023.03.006
H. Hao, Y. Geng, and W. Hang, “GHG emissions from primary aluminum production in China: Regional disparity and policy implications,” Applied Energy, vol. 166, pp. 264-272, 2016. DOI: https://doi.org/10.1016/j.apenergy.2015.05.056
P. E. Tsakiridis, “Aluminium salt slag characterization and utilization – A review,” Journal of Hazardous Materials, vol. 217-218, pp. 1-10, 2012. DOI: https://doi.org/10.1016/j.jhazmat.2012.03.052
C. Dai, and D. Apelian, “Fabrication and characterization of aluminum dross-containing mortar composites: Upcycling of a waste product,” Journal of Sustainable Metallurgy, vol. 3, no. 2, pp. 230-238, 2016.
H. Shen, B. Liu, C. Ekberg, and S. Zhang, “Harmless disposal and resource utilization for secondary aluminum dross: A review,” Science of the Total Environment, vol. 760, 2021. DOI: https://doi.org/10.1016/j.scitotenv.2020.143968
A. Meshram, and K. K. Singh, “Recovery of valuable products from hazardous aluminum dross: A review. Resources,” Conservation and Recycling, vol. 130, pp. 95-108, 2018. DOI: https://doi.org/10.1016/j.resconrec.2017.11.026
X. Zhu, J. Yang, Y. Yang, Q. Huang, and T. Liu, “Pyro-metallurgical process and multipollutant co-conversion for secondary aluminum dross: A review,” Journal of Materials Research and Technology, vol. 21, pp. 1196-1211, 2022. DOI: https://doi.org/10.1016/j.jmrt.2022.09.089
C. Wang, S. Li, Y. Guo, Y. Y. He, J. Liu, and H. Liu, “Comprehensive treatments of aluminum dross in China: A critical review,” Journal of Environmental Management, vol. 345, p. 118575, 2023. DOI: https://doi.org/10.1016/j.jenvman.2023.118575
M. Mahinroosta, and A. Allahverdi, “Hazardous aluminum dross characterization and recycling strategies: A critical review,” Journal of Environmental Management, vol. 223, pp. 452-468, 2018. DOI: https://doi.org/10.1016/j.jenvman.2018.06.068
C. Dai, and D. Apelian, “Fabrication and characterization of aluminum dross-containing mortar composites: upcycling of a waste product,” Journal of Sustainable Metallurgy, vol.3, no. 2, pp. 230-238, 2017. DOI: https://doi.org/10.1007/s40831-016-0071-7
J. Ayawanna, and A. Poowancum, “Enhancing flexural strength of metakaolin-based geopolymer reinforced with different types of fibers,” Sustainable Chemistry and Pharmacy, vol. 37, p. 101439, 2024. DOI: https://doi.org/10.1016/j.scp.2024.101439
T. H. Tan, K. H. Mo, S. H. Lai, and T. C. Ling, “Synthesis of porous geopolymer sphere for Ni(II) removal,” Ceramics International, vol. 47, no. 20, pp. 29055-29063, 2021. DOI: https://doi.org/10.1016/j.ceramint.2021.06.268
S. Chokkha, “Effect of fly ash on compressive strength of metakaolin based geopolymer,” Applied Mechanics and Materials, vol. 873, pp. 170-175, 2017. DOI: https://doi.org/10.4028/www.scientific.net/AMM.873.170
Y. Ettahiri, B. Bouargane, K. Fritah, B. Akhsassi, L. Pérez-Villarejo, A. Aziz, L. Bouna, A. Benlhachemi, and R. M. Novais, “A state-of-the-art review of recent advances in porous geopolymer: Applications in adsorption of inorganic and organic contaminants in water,” Construction and Building Materials, vol.395, p. 132269, 2023. DOI: https://doi.org/10.1016/j.conbuildmat.2023.132269
S. Prasanphan, A. Wannagon, T. Kobayashi, and S. Jiemsirilers, “Reaction mechanisms of calcined kaolin processing waste-based geopolymers in the presence of low alkali activator solution,” Construction and Building Materials, vol. 221, pp. 409-420, 2019. DOI: https://doi.org/10.1016/j.conbuildmat.2019.06.116
B. O. Adeleke, J. M. Kinuthia, J. Oti, and M. Ebailila, “Physico-mechanical evaluation of geopolymer concrete activated by sodium hydroxide and silica fume-synthesised sodium silicate solution,” Materials, vol.16, no. 6, p. 2400, 2023. DOI: https://doi.org/10.3390/ma16062400
S. H. G. Mousavinejad, and M. Sammak, “An assessment of the effect of Na2SiO3/NaOH ratio, NaOH solution concentration, and aging on the fracture properties of ultra-high-performance geopolymer concrete: The application of the work of fracture and size effect methods,” Structures, vol. 39, pp. 434-443, 2022. DOI: https://doi.org/10.1016/j.istruc.2022.03.045
Y. Watanabe, and T. Kobayashi, “Synthesis and characterization of metakaolin-based crystalline phase sodium aluminum silicon oxide geopolymers using concentrated alkaline medium,” Ceramics International, vol. 48, no. 24, pp. 37448-37452, 2022. DOI: https://doi.org/10.1016/j.ceramint.2022.07.280
U. C. C. S. Siciliano, J. Zhao, A. C. C. Trindade, M. Liebscher, V. Mechtcherine, and F. D. A. Silva, “Influence of curing temperature and pressure on the mechanical and microstructural development of metakaolin-based geopolymers,” Construction and Building Materials, vol. 424, no.19, p.135852, 2024. DOI: https://doi.org/10.1016/j.conbuildmat.2024.135852
J. Liu, X. Shi, G. Zhang, and L. Li, “Study the mechanical properties of geopolymer under different curing conditions,” Minerals, vol. 13, no.5, p. 690, 2023. DOI: https://doi.org/10.3390/min13050690
A. Yilmaz, F. N. Degirmenci, and Y. Aygörmez, “Effect of initial curing conditions on the durability performance of low-calcium fly ash-based geopolymer mortars,” Boletín de la Sociedad Española de Cerámica y Vidrio, 2023. DOI: https://doi.org/10.1016/j.bsecv.2023.10.006
C. Bai, and P. Colombo, “Processing, properties and applications of highly porous geopolymers: A review,” Ceramics International, vol. 44, pp. 16103-16118, 2018. DOI: https://doi.org/10.1016/j.ceramint.2018.05.219
R. M. Novais, R. C. Pullar, and J. A. Labrincha, “Geopolymer foams: An overview of recent advancements,” Progress in Materials Science, vol. 109, pp. 100621, 2020. DOI: https://doi.org/10.1016/j.pmatsci.2019.100621
E. Kamseu, B. Nait-Ali, M. C. Bignozzi, C. Leonelli, S. Rossignol, and D. S. Smith, “Bulk composition and microstructure dependence of effective thermal conductivity of porous inorganic polymer cements,” Journal of the European Ceramic Society, vol. 32, no. 8, pp. 1593-1603, 2012. DOI: https://doi.org/10.1016/j.jeurceramsoc.2011.12.030
P. Chindaprasirt, and U. Rattanasak, “Characterization of porous alkali-activated fly ash composite as a solid absorbent,” International Journal of Greenhouse Gas Control, vol. 85, pp. 30-35, 2019. DOI: https://doi.org/10.1016/j.ijggc.2019.03.011
D. Kioupis, A. Zisimopoulou, S. Tsivilis, and G. Kakali, “Development of porous geopolymers foamed by aluminum and zinc powders,” Ceramics International, vol. 47, no. 18, 2021. DOI: https://doi.org/10.1016/j.ceramint.2021.06.037
V. Vaou, and D. Panias, “Thermal insulating foamy geo-polymers from perlite,” Minerals Engineering, vol. 23, no. 14, pp. 1146-1151, 2010. DOI: https://doi.org/10.1016/j.mineng.2010.07.015
S. Yan, X. Ren, W. Wang, C. He, and P. Xing, “Preparation of eco-friendly porous ceramic with low thermal conductivity by high-temperature treatment of foamed solid waste based geopolymer with cenospheres,” Construction and Building Materials, vol. 398, pp. 131190, 2023. DOI: https://doi.org/10.1016/j.conbuildmat.2023.131190
V. Medri, E. Papa, J. Dedecek, H. Jirglova, P. Benito A. Vaccari, and E. Landi, “Effect of metallic Si addition on polymerization degree of in situ foamed alkali-aluminosilicates.” Ceramics International, vol. 39, no. 7, pp. 7657-7668, 2013. DOI: https://doi.org/10.1016/j.ceramint.2013.02.104
C. Zoude, L. Gremillard, and E. P. Homme, “Combination of chemical foaming and direct ink writing for lightweight geo-polymers,” Open Ceramics, vol. 16, no.14, p. 100478, 2023. DOI: https://doi.org/10.1016/j.oceram.2023.100478
W. Sornlar, A. Wannagon, and S. Supothina, “Stabilized homogeneous porous structure and pore type effects on the properties of lightweight kaolinite-based geopolymers,” Journal of Building Engineering, vol. 44, p.103273, 2021. DOI: https://doi.org/10.1016/j.jobe.2021.103273
S. Sanguanpak, A. Wannagon, C. Saengam, W. Chiemchaisri, and C. Chiemchaisri, “Porous metakaolin-based geopolymer granules for removal of ammonium in aqueous solution and anaerobically pretreated piggery wastewater,” Journal of Cleaner Production, vol. 297, p. 126643, 2021. DOI: https://doi.org/10.1016/j.jclepro.2021.126643
N. A. Jaya, L. Y. Ming, H. C. Yong, M. M. A. B. Abdullah, and K. Hussin, “Correlation between pore structure, compressive strength and thermal conductivity of porous metakaolin geopolymer,” Construction and Building Materials, vol .247, p. 118641, 2020.
J. Fiset, M. Cellier, and P. Y. Vuillaume, “Macroporous geopolymers designed for facile polymers post-infusion,” Cement and Concrete Composites, vol. 110, p. 103591, 2020. DOI: https://doi.org/10.1016/j.cemconcomp.2020.103591
F. Xu, G. Gu, W. Zhang, H. Wang, X. Huang, and J. Zhu, “Pore structure analysis and properties evaluations of fly ash-based geopolymer foams by chemical foaming method,” Ceramics International, vol. 44, no. 16, pp.19989-19997, 2018. DOI: https://doi.org/10.1016/j.ceramint.2018.07.267
X. Liu, C. Hu, and L. Chu, “Microstructure, compressive strength and sound insulation property of fly ash-based geo-polymeric foams with silica fume as foaming agent,” Materials, vol. 13, no. 14, p. 3215, 2020. DOI: https://doi.org/10.3390/ma13143215
D. Wattanasiriwech, K. Yomthong, and S. Wattanasiriwech, “Characterisation and properties of class C-fly ash based geopolymer foams: Effects of foaming agent content, aggregates, and surfactant,” Construction and Building Materials, vol. 306, p. 124847, 2021. DOI: https://doi.org/10.1016/j.conbuildmat.2021.124847
N. A. Jaya, L. Y. Ming, H. C. Yong, M. M. A. B. Abdullah, and K. Hussin, “Correlation between pore structure, compressive strength and thermal conductivity of porous metakaolin geo-polymer,” Construction and Building Materials, vol. 247, p. 118641 , 2020. DOI: https://doi.org/10.1016/j.conbuildmat.2020.118641
G. Masi, W. D.A. Rickard, L. Vickers, M. C. Bignozzi, and A. V. Riessen, “A comparison between different foaming methods for the synthesis of light weight geopolymers,” Ceramics International,” vol. 40, no. 9, pp. 13891-13902, 2014. DOI: https://doi.org/10.1016/j.ceramint.2014.05.108
B. Walther, B. Feichtenschlager, and S. Zhou, “Self-foaming Geopolymer Composition Containing Aluminum Dross.” United States Patent, US 9580356 B2. 2017.
G. Bumanis, D. Bajare, A. Korjakins, and D. Vaičiukynienė, “Sulfate and freeze-thaw resistance of porous geopolymer based on waste clay and aluminum salt slag,” Minerals, vol. 12, p. 1140, 2022. DOI: https://doi.org/10.3390/min12091140
C. Leiva, Y. Luna-Galiano, C. Arenas, B. Alonso-Fariñas, and C. Fernández-Pereira, “A porous geopolymer based on aluminum-waste with acoustic properties,” Waste Management, vol. 95, pp. 504-512, 2019. DOI: https://doi.org/10.1016/j.wasman.2019.06.042
A. Maldonado-Alameda, J. Mañosa, T. López-Montero, R. Catalán-Parra, and J. M. Chimenos, “High-porosity alkali-activated binders based on glass and aluminum recycling industry waste,” Construction and Building Materials, vol. 400, 2023. DOI: https://doi.org/10.1016/j.conbuildmat.2023.132741
H. Majdoubi, Y. Haddaji, O. Bourzik, M. Nadi, J. Ziraoui, T. S. Alomayri, M. Oumam, B. Manoun, J. Alami, Y. Tamraoui,
and H. Hannache, “Enhancing thermal insulation with phosphate
washing sludge waste as an inorganic foaming agent in porous acid-based geopolymers: Formulation and processing optimization,” Construction and Building Materials, vol. 407, 2023. DOI: https://doi.org/10.1016/j.conbuildmat.2023.133486
A. Poowancum, and P. Aengchuan, “Utilization of low reactivity fly ash for fabricating geopolymer materials,” Advances in Cement Research, vol. 35, no. 3, pp. 1-21, 2022. DOI: https://doi.org/10.1680/jadcr.21.00025
ASTM C266-21, “Standard Test Method for Time of Setting of Hydraulic-Cement Paste by Gillmore Needles,” In: Annual Book of ASTM Standard, ASTM International, West Conshohocken, PA, USA, 2021.
D. Wang, and L. S. Fan, “Particle characterization and behavior relevant to fluidized bed combustion and gasification systems,” In Fluidized Bed Technologies for Near-Zero Emission Combustion and Gasification, pp. 42-76, 2013. DOI: https://doi.org/10.1533/9780857098801.1.42
ASTM C642-13, “Standard Test Method for Density, Absorption, and Voids in Hardened Concrete,” In: Annual Book of ASTM Standard, ASTM International, West Conshohocken, PA, USA, 2013.
ASTM C109/C109M-20, “Standard Test Method for Compressive Strength of Hydraulic Cement Mortars (Using 2-in. or [50-mm] Cube Specimens),” In: Annual Book of ASTM Standard, ASTM International, West Conshohocken, PA, USA, 2020.
B. R. Das, B. Dash, B. C. Tripathy, I. N. Bhattacharya, and S. C. Das, “Production of η-alumina from waste aluminium dross,” Minerals Engineering, vol. 20, no. 3, pp. 252-258, 2007. DOI: https://doi.org/10.1016/j.mineng.2006.09.002
E. Nimwinya, W. Arjharn, S. Horpibulsuk, T. Phoo-ngernkham, and A. Poowancum, “A sustainable calcined water treatment sludge and rice husk ash geopolymer,” Journal of Cleaner Production, vol. 119, pp. 128-134, 2016. DOI: https://doi.org/10.1016/j.jclepro.2016.01.060
ASTM C150/C150M-20, “Standard Specification for Portland Cement,” In: Annual Book of ASTM Standard, ASTM International, West Conshohocken, PA, USA, 2020.
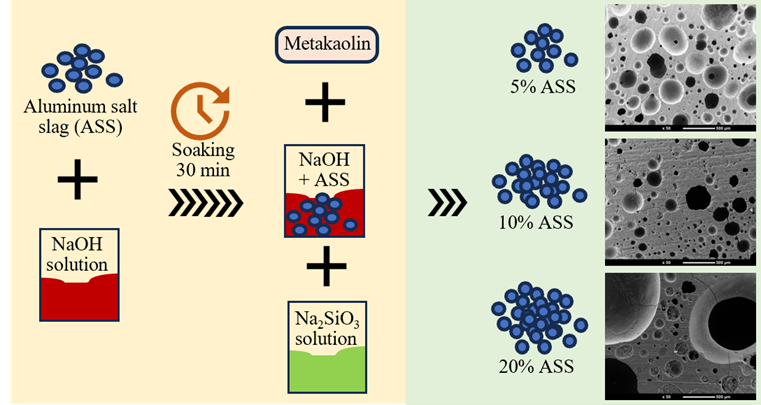
Downloads
Published
How to Cite
Issue
Section
Categories
License
Copyright (c) 2024 Journal of Metals, Materials and Minerals

This work is licensed under a Creative Commons Attribution-NonCommercial-NoDerivatives 4.0 International License.
Authors who publish in this journal agree to the following terms:
- Authors retain copyright and grant the journal right of first publication with the work simultaneously licensed under a Creative Commons Attribution License that allows others to share the work with an acknowledgment of the work's authorship and initial publication in this journal.
- Authors are able to enter into separate, additional contractual arrangements for the non-exclusive distribution of the journal's published version of the work (e.g., post it to an institutional repository or publish it in a book), with an acknowledgment of its initial publication in this journal.