Optimized parameter of dissimilar joining between Al6061-T6 and height-strength steel with friction stir spot welding process (FSSW)
DOI:
https://doi.org/10.55713/jmmm.v32i4.1538คำสำคัญ:
Optimized parameter, Dissimilar joining, Friction stir spot weldingบทคัดย่อ
High-strength steel and aluminum alloys are used to manufacture modern vehicles. The objective was to reduce the weight and fuel consumption of the vehicles. In this study the optimum parameters for the friction stir spot welding (FSSW) process between Al6061-T6 aluminum alloy and HSS590 high-strength steel were determined. Response surface methodology based on central composite design (CCD) with three parameters, five levels, and 19 runs was used to conduct experiments and develop mathematical regression models. The three joint parameters were tool speed, welding feed, and dwell time. Analysis of variance was then performed to examine the adequacy of the developed models. Finally, the effects of the process parameters on the mechanical properties were investigated using mathematical models. In addition, the distribution of the chemical composition and fracture characteristics of the joints was examined using scanning electron microscopy (SEM). The investigation found that the optimum welding parameters were a tool speed of 1576 rpm, welding feed rate of 45 mm∙min-1, and dwell time of 10 s. Furthermore, the results confirmed that the mathematical models and experiments were consistent.
Downloads
เอกสารอ้างอิง
Y. C. Chen, A. Gholinia, and P. B. Prangnell, “Interface structure and bonding in abrasion circle friction stir spot welding: a novel approach for rapid welding aluminium alloy to steel automotive sheet,” Materials Chemistry and Physics, vol. 134, no. 1, pp. 459-463, 2012.
S. Bozzi, A. L. Helbert-Etter, T. Baudin, B. Criqui, and J. G. Kerbiguet, “Intermetallic compounds in Al 6016/IF-steel friction stir spot welds,” Materials Science and Engineering: A, vol. 527, no. 16-17, pp. 4505-4509, 2021.
Y. Hovanski, M. L. Santella, and G. J. Grant, “Friction stir spot welding of hot-stamped boron steel,” Scripta Materialia, vol. 57, no. 9, pp. 873-876, 2007.
M. I. Khan, M. L. Kuntz, P. Su, A. Gerlich, T. North, and Y. Zhou, “Resistance and friction stir spot welding of DP600: A comparative study,” Science and Technology of Welding and Joining, vol. 12, no. 2, pp. 175-182, 2007.
S. Prasomthong, and S. Namkeaw, “The Influence of adding aluminum welding wire on mechanical properties and chemical composition of the welding hardfacing welded low carbon steel by gas tungsten arc welding process,” The Journal of Industrial Technology, vol. 15, no. 1, pp. 27-36, 2019.
M. Santella, Y. Hovanski ,and T. Y. Pan, “Friction stir spot welding (FSSW) of advanced high strength steel (AHSS),” SAE International Journal of Materials and Manufacturing, vol. 5, no. 2, pp. 382-387, 2012.
Y. Tozaki, Y. Uematsu, and K. Tokaji, “A newly developed tool without probe for friction stir spot welding and its performance,” Journal of Materials Processing Technology, vol. 210, no. 6-7, pp. 844-851, 2010.
C. Y. Lee, D. H. Choi, Y. M. Yeon, and S. B. Jung, “Dissimilar friction stir spot welding of low carbon steel and Al-Mg alloy by formation of IMCs,” Science and Technology of Welding and Joining, vol. 14, no. 3, pp. 216-220, 2009.
T. Liyanage, J. Kilbourne, A. P. Gerlich, and T. H. North, “Joint formation in dissimilar Al alloy/steel and Mg alloy/steel friction stir spot welds,” Science and Technology of Welding and Joining, vol.14, no. 6, pp. 500-508, 2009.
K. Nakowong, and K. Sillapasa, “Optimized parameter for butt joint in friction stir welding of semi-solid aluminum alloy 5083 using taguchi technique,” Journal of Manufacturing and Materials Processing, vol. 5, no. 3, pp. 1-21, 2021.
S. M. M. Zamani, K. Behdinan, M. R. Razfar, D. H. Fatmehsari, and J. A. Mohandesi, “Studying the effects of process parameters on the mechanical properties in friction stir welding of Al-SiC composite sheets,” The International Journal of Advanced Manufacturing Technology, vol. 113, no. 11, pp. 3629-3641, 2011.
M. MohammadiSefat, H. Ghazanfari, and C. Blais, “Friction stir welding of 5052-H18 aluminum alloy: Modeling and process parameter optimization,” Journal of Materials Engineering and Performance, vol. 30, no. 3, pp.1838-1850, 2021.
M. F. Naqibi, M. Elyasi, H. J. Aval, and M. J. Mirnia, “Statistical modeling and optimization of two-layer aluminum-copper pipe fabrication by friction stir welding,” Transactions of the Indian Institute of Metals, vol. 75, no. 3, pp.635-651, 2022.
P. Kumar, and S. Sharma, “Influence of FSW process parameters on formability and mechanical properties of tailor welded blanks AA6082-T6 and AA5083-O using RSM with GRA-PCA approach,” Transactions of the Indian Institute of Metals, vol. 74, no. 8, pp. 1943-1968, 2021.
D. Chakradhar, and S. Narendranath, “Analysis of the effect of friction stir welding parameters on characteristics of AA6061 composites using response surface methodology,” Transactions of the Indian Institute of Metals, vol. 74, no. 6, pp. 1303-1319, 2021.
R. Mirabzadeh, V. Parvaneh, and A. Ehsani, “Experimental and numerical investigation of the generated heat in polypropylene sheet joints using friction stir welding (FSW),” International Journal of Material Forming, vol. 14, no. 5, pp. 1067-1083, 2021.
M. Ahmadnia, S. Shahraki, and M. A. Kamarposhti, “Experimental studies on optimized mechanical properties while dissimilar joining AA6061 and AA5010 in a friction stir welding process,” The International Journal of Advanced Manufacturing Technology, vol. 87, no. 5, pp. 2337-2352, 2016.
G. Yu, X.Chen, B. Zhang, K. Pan, and L. Yang, “Tensile-shear mechanical behaviors of friction stir spot weld and adhesive hybrid joint : Experimental and numerical study,” Metals, vol. 10, no. 8, pp. 1028, 2020.
S. Prasomthong, and S.Charoenrat, “The optimization of welding hardfacing on wear resistance of FC-25 grey cast iron steel substrate by response surface methodology (RSM),” SNRU Journal of Science and Technology, vol. 14, no. 2, pp. 1-8, 2022
S. Charoenrat, and S. Prasomthong, “Consideration of the optimizing condition in welding hardfacing on wear resistance with hot-wire gas tungsten arc welding process by response surface methodology (RSM),” The Journal of Industrial Technology, vol. 17, no. 2, pp. 87-102, 2021.
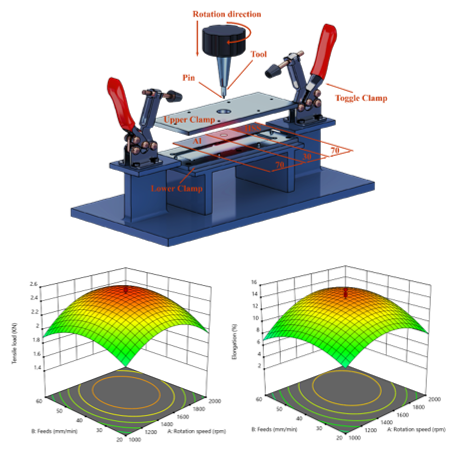
ดาวน์โหลด
เผยแพร่แล้ว
วิธีการอ้างอิง
ฉบับ
บท
การอนุญาต
ลิขสิทธิ์ (c) 2022 วารสารโลหะ, วัสดุ และแร่

This work is licensed under a Creative Commons Attribution-NonCommercial-NoDerivatives 4.0 International License.
Authors who publish in this journal agree to the following terms:
- Authors retain copyright and grant the journal right of first publication with the work simultaneously licensed under a Creative Commons Attribution License that allows others to share the work with an acknowledgment of the work's authorship and initial publication in this journal.
- Authors are able to enter into separate, additional contractual arrangements for the non-exclusive distribution of the journal's published version of the work (e.g., post it to an institutional repository or publish it in a book), with an acknowledgment of its initial publication in this journal.