Effect of hatch spacing in selective laser melting process of Ti-6Al-4V alloy on finished surface roughness: A computational study
DOI:
https://doi.org/10.55713/jmmm.v34i3.1861คำสำคัญ:
Selective laser melting, Overlap, Multi-tracks, CFD simulation, Ti-6Al-4Vบทคัดย่อ
The Selective Laser Melting (SLM) process is a promising additive manufacturing technology for producing complex metal parts. However, this process has certain limitations, including lack of fusion and defects, which can hinder its industrial applications. These challenges can be addressed by determining the appropriate overlap percentage parameters. This study used numerical simulation to explore the effect of overlap percentage on multi-track melting in the SLM process for Ti-6Al-4V. The simulation results categorize the multi-track melting morphologies into two distinct groups. The first group, (0% to 40% overlap), displays consistent surface roughness with an average Ra value of 7 µm. In contrast, the second group (50% to 60% overlap), shows non-uniform shapes. Specifically, the three central tracks in this group present an Ra value of approximately 4 µm. However, when all five tracks of this group are taken into account, the average Ra rises to 14 µm. These differences in surface roughness can be attributed to factors like energy density and the Marangoni effect. Both melt pool depth and shrinkage depth in the overlap area are significant as they might contribute to the risk of the lack of fusion defects. The insights from this research hold potential in shaping scanning pattern strategy design.
Downloads
เอกสารอ้างอิง
D. Dong, C. Chang, H. Wang, X. Yan, W. Ma, M. Liu, S. Deng, J. Gardan, R. Bolot, and H. Liao, “Selective laser melting (SLM) of CX stainless steel: Theoretical calculation, process optimization and strengthening mechanism”, Journal of Materials Science & Technology, vol. 73, pp. 151-164, 2021. DOI: https://doi.org/10.1016/j.jmst.2020.09.031
S. Chowdhury, N. Yadaiah, C. Prakash, S. Ramakrishna, S. Dixit, L. R. Gupta, and D. Buddhi, “Laser powder bed fusion: a state-of-the-art review of the technology, materials, properties & defects, and numerical modelling”, Journal of Materials Research and Technology, vol. 20, pp. 2109 – 2172, 2022. DOI: https://doi.org/10.1016/j.jmrt.2022.07.121
M. Bayat, W. Dong, J. Thorborg, A. C. To, and J. H. Hattel, “A review of multi-scale and multi-physics simulations of metal additive manufacturing processes with focus on modeling strategies”, Additive Manufacturing. vol. 47, 102278, 2021. DOI: https://doi.org/10.1016/j.addma.2021.102278
M. Bayat, S. Mohanty, and J. H. Hattel, “Multiphysics modelling of lack-of-fusion voids formation and evolution in IN718 made by multi-track/multi-layer L-PBF”, International Journal of Heat and Mass Transfer. vol. 139, pp. 95-114, 2019. DOI: https://doi.org/10.1016/j.ijheatmasstransfer.2019.05.003
W. Ge, J. Y. H. Fuh, and S. J. Na, “Numerical modelling of keyhole formation in selective laser melting of Ti6Al4V”, Journal of Manufacturing Processes, vol. 62, pp. 646–654, 2021. DOI: https://doi.org/10.1016/j.jmapro.2021.01.005
X. Ao, J. Liu, H. Xia, and Y. Yang, “A numerical study on the mesoscopic characteristics of Ti-6Al-4V by selective laser melting,” Materials, vol. 15, no. 8, p. 2850, 2022. DOI: https://doi.org/10.3390/ma15082850
W. Wang, and S. Y. Liang, “Prediction of molten pool height, contact angle, and balling occurrence in laser powder bed fusion”. The International Journal of Advanced Manufacturing Technology, vol. 119, pp. 6193-6202, 2022. DOI: https://doi.org/10.1007/s00170-021-08633-8
B. Liu, G. Fang, L. Lei, and W. Liu, “Experimental and numerical exploration of defocusing in Laser Powder Bed Fusion (LPBF) as an effective processing parameter”, Optics & Laser Technology, vol. 149, 2022. DOI: https://doi.org/10.1016/j.optlastec.2022.107846
W. Yuan, H. Chen, T. Cheng, and Q. Wei, “Effects of laser scanning speeds on different states of the molten pool during selective laser melting: Simulation and experiment”. Materials & Design. vol. 189, p. 108542, 2020.
Y. Tian, L. Yang, D. Zhao, Y. Huang, and J. Pan, “Numerical analysis of powder bed generation and single track forming for selective laser melting of SS316L stainless steel”. Journal of Manufacturing Processes, vol. 58, pp. 964-974, 2020. DOI: https://doi.org/10.1016/j.jmapro.2020.09.002
M. Zheng, L. Wei, J. Chen, Q. Zhang, G. Zhang, X. Lin, and W. Huang, “On the role of energy input in the surface morphology and microstructure during selective laser melting of Inconel 718 alloy”, Journal of Materials Research and Technology, vol. 11, 2021. DOI: https://doi.org/10.1016/j.jmrt.2021.01.024
K. Mahyar, G. AmirHossein, L. Martin, O. William, G. Ian, C. Laura, and R. Bernard, “Numerical and analytical investigation on meltpool temperature of laser-based powder bed fusion of IN718”, International Journal of Heat and Mass Transfer, vol. 177, 2021. DOI: https://doi.org/10.1016/j.ijheatmasstransfer.2021.121477
Z. Wang, W. Yan, W. Liu, and M. Liu, “Powder-scale multi-physics modeling of multi-layer multi-track selective laser melting with sharp interface capturing method”, Computational Mechanics, vol. 63, pp. 649-661, 2019.
F. Ali, B. Mohsen, F. Ehsan, and G. Sa’id, “finite element simulation of selective laser melting process considering optical penetration depth of laser in powder bed”, Materials & Design, vol. 89, pp. 255-263, 2016. DOI: https://doi.org/10.1016/j.matdes.2015.10.002
Z. Dong, Y. Liu, W. Wen, J. Ge, and J. Liang, “Effect of hatch spacing on melt pool and as-built quality during selective laser melting of stainless steel: Modeling and experimental approaches”, Materials, vol. 12, no. 1, pp. 50, 2018. DOI: https://doi.org/10.3390/ma12010050
H. Gu, C. Wei, L. Li, Q. Han, R. Setchi, M. Ryan, and Q. Li, “Multi-physics modelling of molten pool development and track formation in multi-track, multi-layer and multi-material selective laser melting”, International Journal of Heat and Mass Transfer, vol. 151, 2020. DOI: https://doi.org/10.1016/j.ijheatmasstransfer.2020.119458
P. Laakso, T. Riipinen, A. Laukkanen, T. Andersson, A. Jokinen, A. Revuelta, and K. Ruusuvuori, “Optimization and simulation of slm process for high density H13 tool steel parts”, Physics Procedia, vol. 83, pp. 26-35, 2016. DOI: https://doi.org/10.1016/j.phpro.2016.08.004
T. Zakrzewski, J. Kozak, M. Witt, and M. Dębowska-Wąsak, “Dimensional analysis of the effect of SLM parameters on surface roughness and material density”, Procedia CIRP 95, pp. 115-120, 2020. DOI: https://doi.org/10.1016/j.procir.2020.01.182
Z. Wang, W. Yan, W. K. Liu, M. Liu, “Powder-scale multi-physics modeling of multi-layer multi-track selective laser melting with sharp interface capturing method”, Computational Mechanics, vol. 63, pp. 649-661, 2019. DOI: https://doi.org/10.1007/s00466-018-1614-5
M. M. Basha, S. M. Basha, V. K. Jain, and M. R. Sankar, “State of the art on chemical and electrochemical based finishing processes for additive manufactured features”, Additive Manufacturing, vol. 58, 103028, 2022. DOI: https://doi.org/10.1016/j.addma.2022.103028
J. Song, Q. Tang, Q. Feng, S. Ma, Q. Han, and R. Setchi, “Effect of remelting process on surface quality and tensile behaviour of a maraging steel manufactured by selective laser melting”, Sustainable Design and Manufacturing (Conference paper), pp. 251-260, 2020. DOI: https://doi.org/10.1007/978-981-15-8131-1_23
C. Veiga, J. P. Davim, and A. J. R. Loureiro, “Properties and applications of titanium alloys: A brief review”, Reviews on advanced materials science, vol. 32, pp. 133- 148, 2012.
V. Chastand, P. Quaegebeur, W. Maia, and E. Charkaluk, “Comparative study of fatigue properties of Ti-6Al-4V specimens built by electron beam melting (EBM) and selective laser melting (SLM)”, Materials Characterization, vol. 143, pp. 76-81, 2018. DOI: https://doi.org/10.1016/j.matchar.2018.03.028
C. Bo, L. Xiaobai, T. Charles, I. Alexander, W. Hannes, and H. Udo, “Multi-physics modeling of single track scanning in selective laser melting: powder compaction effect”. Proc. of the 29th Annual International Solid Freeform Fabrication Symposium – An Additive Manufacturing Conference, August 13-15, 2018, Austin, TX, USA, pp. 1887-1902
X. Shan., Z. Pan., M. Gao., L. Han., J. P. Choi., and H. Zhang., “Multi-physics modeling of melting-solidification characteristics in laser powder bed fusion process of 316L stainless steel”, Materials, vol. 17, No. 4:946, pp. 1-13, 2024. DOI: https://doi.org/10.3390/ma17040946
W. Wang., W. Lin., R. Yang., Y. Wu., J. Li., Zh. Zhang, and Z. Zhai., “Mesoscopic evolution of molten pool during selective laser melting of superalloy Inconel 738 at elevating preheating temperature”, Materials & Design, vol. 213, 110355, 2022. DOI: https://doi.org/10.1016/j.matdes.2021.110355
H. Li, X. Liang, Y. Li, and F. Lin, “Performance of high-layer-thickness Ti6Al4V fabricated by electron beam powder bed fusion under different accelerating voltage values,” Materials, vol. 15, no. 5, pp. 1878, 2022. DOI: https://doi.org/10.3390/ma15051878
P. Ninpetch, P. Chalermkarnnon, and P. Kowitwarangkul, “Multiphysics simulation of thermal‑fluid behavior in laser powder bed fusion of H13 Steel: Influence of layer thickness and energy input”, Metals and Materials International, vol. 29, pp. 536-551, 2023. DOI: https://doi.org/10.1007/s12540-022-01239-z
Y. Weihao, C. Hui, C. Tan, and W. Qingsong, “Effects of laser scanning speeds on different states of the molten pool during selective laser melting: Simulation and experiment”, Materials & Design, vol. 189, p. 108542, 2020. DOI: https://doi.org/10.1016/j.matdes.2020.108542
C. H. Fu, and Y. B. Guo, “Three-dimensional temperature gradient mechanism in selective laser melting of Ti-6Al-4V”, ASME. Journal of Manufacturing Science and Engineering, vol. 136, no. 6, 061004, 2014. DOI: https://doi.org/10.1115/1.4028539
K. C. Mills, “Recommended values of thermophysical properties for selected commercial alloys”, A volume in Woodhead Publishing Series in Metals and Surface Engineering, pp. 211-217, 2002. DOI: https://doi.org/10.1533/9781845690144.211
S. B. Umberto,. W. J. Alexander, J. M. Manyalibo, R. De. Jean-Pierre, and M. S. Julie, “On the limitations of volumetric energy density as a design parameter for selective laser melting”, Materials & Design, vol. 113, pp. 331-340, 2017. DOI: https://doi.org/10.1016/j.matdes.2016.10.037
D. Kouprianoff, I. Yadroitsava, A. du Plessis, N. Luwes and I. Yadroitsev, “Monitoring of laser powder bed fusion by acoustic emission: investigation of single tracks and layers”, Frontiers in Mechanical Engineering, vol. 7, p. 678076, 2021. DOI: https://doi.org/10.3389/fmech.2021.678076
D. Chen, G. Li, P. Wang, Z. Zeng, and Y. Tang “Numerical simulation of melt pool size and flow evolution for laser powder bed fusion of powder grade ti6al4v,” Finite Elements in Analysis and Design, 223, pp. 103971, 2023. DOI: https://doi.org/10.1016/j.finel.2023.103971
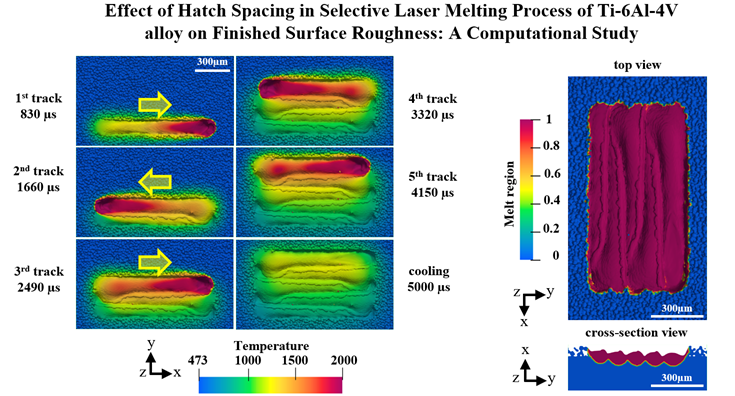
ดาวน์โหลด
เผยแพร่แล้ว
วิธีการอ้างอิง
ฉบับ
บท
การอนุญาต
ลิขสิทธิ์ (c) 2024 วารสารโลหะ, วัสดุ และแร่

This work is licensed under a Creative Commons Attribution-NonCommercial-NoDerivatives 4.0 International License.
Authors who publish in this journal agree to the following terms:
- Authors retain copyright and grant the journal right of first publication with the work simultaneously licensed under a Creative Commons Attribution License that allows others to share the work with an acknowledgment of the work's authorship and initial publication in this journal.
- Authors are able to enter into separate, additional contractual arrangements for the non-exclusive distribution of the journal's published version of the work (e.g., post it to an institutional repository or publish it in a book), with an acknowledgment of its initial publication in this journal.