Enhancing the efficiency of hemp fiber dyeing with natural dyes: Indigo and lac
DOI:
https://doi.org/10.55713/jmmm.v34i2.1873คำสำคัญ:
Hemp fibers, Natural dyes, Mercerization, Cationization, Fiber treatment, Indigo, Lacบทคัดย่อ
Hemp fibers dyed with natural dyes are environmentally sustainable, but it is typically difficult to achieve an intense shade and washing durability. In this study, mercerization and cationization using polyelectrolyte, Poly-diallyldimethylammonium chloride (polyDADMAC), were chosen to enhance the dyeing efficiency and mechanical properties. Indigo and lac were chosen as natural dyes due to their widespread use. SEM demonstrated that untreated fibers contained the non-cellulose boundary layer on the surfaces, but after mercerization, the surfaces were smoother, making them suitable for absorbing natural dyes. In agreement with the FT-IR, the spectra of non-cellulose disappeared after mercerizing. Following cationization, the FT-IR spectra confirmed the consequences of using poly-DADMAC. Tensile testing demonstrated that mercerized hemp yarns were 34.1% stronger compared to untreated hemp yarns due to the decrease in non-cellulose content and that the intermolecular attraction of cellulose was not disturbed. The color strength and fastness properties were described by the K/S value. Mercerization considerably affected the K/S of indigo dyeing, while cationization affected lac dyeing significantly. Besides that, both treatments improved fastness properties as well.
Downloads
เอกสารอ้างอิง
A. K. Jakubowska, E. Bogacz, and M. Zimniewska, “Review of natural fibers: part 1-vegetable fibers,” Journal of Natural Fibers, vol. 9, pp. 150-167, 2012. DOI: https://doi.org/10.1080/15440478.2012.703370
H. R. Kymalainen, and A. M. Sjoberg, “Flax and hemp fibres as raw materials for thermal insulations,” Building and Environment, vol. 43, pp. 1261-1269, 2008. DOI: https://doi.org/10.1016/j.buildenv.2007.03.006
F. Ahmed, and I. H. Mondal, “Introduction to natural fibres and textiles,” In Fundamentals of Natural Fibres and Textiles, I. H. Mondal Ed.: Woodhead Publishing, 2021, pp. 1-30. DOI: https://doi.org/10.1016/B978-0-12-821483-1.00001-2
J. Ampruk, Forensic analyses natural and synthetic fibers using FT-IR spectroscopy. Nakhon Pathom: Silpakorn University, 2012.
R. Zah, R. Hischier, A. L. Leao, and I. Braun, “Curaua´ fibers in the automobile industry-a sustainability assessment,” Journal of Cleaner Production, vol. 15, pp. 1032-1040, 2007. DOI: https://doi.org/10.1016/j.jclepro.2006.05.036
C. Lopez, B. Novales, H. Rabesona, M. Weber, T. Chardot, and M. Anton, “Deciphering the properties of hemp seed oil bodies for food applications: lipid composition, microstructure, surface properties and physical stability,” Food Research International Journal, vol. 150, p. 110759, 2021. DOI: https://doi.org/10.1016/j.foodres.2021.110759
M. Kowalska, M. Ziomek, and A. Zbikowska, “Stability of cosmetic emulsion containing different amount of hemp oil,” International Journal of Cosmetic Science, vol. 37, pp. 408-416, 2013. DOI: https://doi.org/10.1111/ics.12211
R. Paul, R. Williams, V. Hodson, and C. Peake, “Detection of cannabinoids in hair after cosmetic application of hemp oil,” Scientific Reports, vol. 9, p. 2582, 2019. DOI: https://doi.org/10.1038/s41598-019-39609-0
T. Morenoa, F. Montanes, S. J. Tallona, T. Fentona, and J. W. King, “Extraction of cannabinoids from hemp (cannabis sativa l.) using high pressure solvents: an overview of different processing options,” Journal of Supercritical Fluids, vol. 161, p. 104850, 2020. DOI: https://doi.org/10.1016/j.supflu.2020.104850
R. L. Hilderbrand, “Hemp & Cannabidiol: what is a medicine?,” Missouri Medicine, vol. 115, pp. 306-309, 2018.
N. Lu, and S. Oza, “Thermal stability and thermo-mechanical properties of hemp-high density polyethylene composites: effect of two different chemical modifications,” Composites Part B: Engineering, vol. 44, pp. 484-490, 2013. DOI: https://doi.org/10.1016/j.compositesb.2012.03.024
L. Y. Mwaikambo, and M. P. Ansell, “Mechanical properties of alkali treated plant fibres and their potential as reinforcement materials. I. hemp fibres,” Journal of Materials Science, vol. 41, pp. 2483-2496, 2006. DOI: https://doi.org/10.1007/s10853-006-5098-x
M. J. Al-Kheetan, “Performance improvement of hemp-shiv cementitious composites through hot water and steam treatment,” Construction and Building Materials, vol. 367, p. 130315, 2023. DOI: https://doi.org/10.1016/j.conbuildmat.2023.130315
G. A. Sivasankar, P. A. Karthick, C. Boopathi, S, Brindha, R. J. T. Nirmalraj, A. Benham, “Evaluation and comparison on mechanical properties of abaca and hemp fiber reinforced hybrid epoxy resin composites,” Materials Today: Proceedings, article in press, 2023. DOI: https://doi.org/10.1016/j.matpr.2023.04.400
A. C. Santos, and P. Archbold, “Suitability of surface-treated flax and hemp fibers for concrete reinforcement,” Fibers, vol. 10, p. 101, 2020. DOI: https://doi.org/10.3390/fib10110101
K. Vandepitte, S. Vasile, S. Vermeire, M. Vanderhoeven, W. V. Borght, J. Latr´e, A. D. Raeve, and V. Troch, “Hemp (cannabis sativa l.) for high-value textile applications: the effective long fiber yield and quality of different hemp varieties, processed using industrial flax equipment,” Industrial Crops and Products, vol. 158, p. 112969, 2020. DOI: https://doi.org/10.1016/j.indcrop.2020.112969
G. Gedik, and O. Avinc, “Hemp usage in textile industry,” In Revolutionizing the Potential of Hemp and Its Products in Changing the Global Economy, T. Belwal and N. C. Belwal Eds.: Springer, 2022, pp. 69-55. DOI: https://doi.org/10.1007/978-3-031-05144-9_4
K. Palanikumar, E. Natarajan, K. Markandan, C. K. Ang, and G.Franz, “Targeted pre-treatment of hemp fibers and the effect on mechanical properties of polymer composites,” Fibers, vol. 11, p. 43, 2023. DOI: https://doi.org/10.3390/fib11050043
M. Zimniewska, “Hemp fibre properties and processing target textile: a review,” Materials, vol. 15, p. 1901, 2022. DOI: https://doi.org/10.3390/ma15051901
S. Balakrishnan, D. Wickramasinghe, and S. Wijayapala, “Study on dyeing behavior of banana fiber with reactive dyes,” Journal of Engineered Fibers and Fabrics, vol. 14, pp. 1-12, 2019. DOI: https://doi.org/10.1177/1558925019884478
X. Yan, L. Hong, S. Pei, A. Hamilton, H. Sun, R. Yang, A. Liu, and L. Yang, “A natural yellow colorant from buddleja officinalis for dyeing hemp fabric,” Industrial Crops and Products, vol. 171, p.113968, 2021. DOI: https://doi.org/10.1016/j.indcrop.2021.113968
D. Grifoni, L. Bacci, G. Zipoli, G. Carreras, S. Baronti, and F. Sabatini, “Laboratory and outdoor assessment of uv protection offered by flax and hemp fabrics dyed with natural dyes,” Photochemistry and Photobiology, vol. 85, pp. 313-320, 2009. DOI: https://doi.org/10.1111/j.1751-1097.2008.00439.x
M. A. Ahmed, and A. A. Mohamed, “A systematic review of layered double hydroxide-based materials for environmental remediation of heavy metals and dye pollutants,” Inorganic Chemistry Communications, vol. 148, p. 110325, 2023. DOI: https://doi.org/10.1016/j.inoche.2022.110325
T. B. Tafesse, A. K. Yetemegne, and S. Kumar, “Analysis of copper, chromium & lead in hawassa and arba minch textile effluents,” Journal of Chemistry and Chemical Sciences, vol. 5, pp. 153-168, 2015.
A. P. Manian, S. Mueller, T. Bechtold, and T. Pham, “Quantification of indigo on denim textiles as basis for jeans recycling,” Dyes and Pigments, vol. 216, p. 111327, 2023. DOI: https://doi.org/10.1016/j.dyepig.2023.111327
R. Santos, J. Hallett, M. C. Oliveira, M. M. Sousa, J. Sarraguça, M. S. J. Simmonds, and M. Nesbitt, “HPLC-DAD-MS analysis of colorant and resinous components of lac-dye: a comparison between kerria and paratachardina genera,” Dyes and Pigments, vol. 118, pp. 129-136, 2015. DOI: https://doi.org/10.1016/j.dyepig.2015.02.024
K. G. Gilbert, H. G. Maule, B. Rudolph, M. Lewis, H. Vandenburg, E. Sales, S. Tozzi, and D. T. Cooke, “Quantitative analysis of indigo and indigo precursors in leaves of isatis spp. and polygonum tinctorium,” Biotechnology Progress, vol. 20, pp. 1289-1292, 2004. DOI: https://doi.org/10.1021/bp0300624
K. Luepong, P. Punyacharoennon, and W. Yimklib, Printing on cotton and polyester by lac dye without mordanting for the small enterprise. Bangkok: Rajamangala University of Technology Phra Nakhon, 2018.
T. Teerakulchaikit, The study and development of outdoor relax furniture from indigo dyed cotton cloth. Nakhon Pathom: Silpakorn University, 2014.
A. Adhikari, S. Mukherjee, A. K. Chakraborty, S. Biswas, A. Basu, C. Chakraborty, S. Chattopadhyay, D. Das, and D. Chattopadhyay, “Lac-extract doped polyaniline nano-ribbons as fluorescence sensor and molecular switch for detection of aqueous AsO43- and Fe3+ contaminants,” Journal of Photo-chemistry and Photobiology A: Chemistry, vol. 431, p. 114000, 2022. DOI: https://doi.org/10.1016/j.jphotochem.2022.114000
B. Dulo, K. Phan, J. Githaiga, K. Raes, and S. D. Meester, “Natural quinone dyes: A review on structure, extraction techniques, analysis and application potential,” Waste and Biomass Valorization, vol. 12, pp. 6339-6374, 2021. DOI: https://doi.org/10.1007/s12649-021-01443-9
S. Yamada, N. Noda, E. Mikami, J. Hayakawa, and M. Yamada, “Analysis of natural coloring matters in food: III. application of methylation with diazomethane for the detection of lac color,” Journal of the Association of Official Analytical Chemists, vol. 72, pp. 48-51, 1989. DOI: https://doi.org/10.1093/jaoac/72.1.48
P. Dagur, and M. Ghosh, “Evaluation of antiproliferative activity of lac dye fractions against mda-mb-231 and siha cell lines,” Anti-Cancer Agents in Medicinal Chemistry, vol. 22, pp. 2577-2585, 2022. DOI: https://doi.org/10.2174/1872210516666220224095221
H. Oka, Y. Ito, S. Yamasa, T. Kagami, J. Hayakawa, K. I. Harada, E. Atsumi, M. Suzuki, M. Suzuki, H. Odani, S. Aka-hori, K. Maeda, H. Nakazawa, and Y. Ito, “Separation of lac dye components by high-speed countercurrent chromatography,” Journal of Chromatography A, vol. 813, p. 71, 1998. DOI: https://doi.org/10.1016/S0021-9673(98)00311-2
M. Chairata, S. Rattanaphania, J. B. Bremnerb, and V. Rattanaphania, “An adsorption and kinetic study of lac dyeing on silk,” Dyes and Pigments, vol. 64, pp. 231-241, 2005. DOI: https://doi.org/10.1016/j.dyepig.2004.06.009
A. P. Periyasamy, “Natural dyeing of cellulose fibers using syzygium cumini fruit extracts and a bio-mordant: a step toward sustainable dyeing,” Sustainable Materials and Technologies, vol. 33, p. e00472, 2022. DOI: https://doi.org/10.1016/j.susmat.2022.e00472
D. Cronier, B. Monties, and B. Chabbert, “Structure and chemical composition of bast fibers isolated from developing hemp stem,” Journal of Agricultural and Food Chemistry, vol. 53, pp. 8279-8289, 2005. DOI: https://doi.org/10.1021/jf051253k
H. M. G. Werf, J. E. H. Veen, A. T. M. Bouma, and M. Cate, “Quality of hemp (cannabis sativa l.) stems as a raw material for paper,” Industrial Crops and Products, vol. 2, pp. 219-227, 1994. DOI: https://doi.org/10.1016/0926-6690(94)90039-6
K. B. Hamou, H. Kaddami, F. Elisabete, and F. Erchiqui, “Synergistic association of wood/hemp fibers reinforcements on mechanical, physical and thermal properties of polypropylene-based hybrid composites,” Industrial Crops and Products, vol. 192, p. 116052, 2023. DOI: https://doi.org/10.1016/j.indcrop.2022.116052
Z. Maa, G. Panb, H. Xua, Y. Huanga, and Y. Yang, “Cellulosic fibers with high aspect ratio from cornhusks via controlled swelling and alkaline penetration,” Carbohydrate Polymers, vol. 124, pp. 50-56, 2015. DOI: https://doi.org/10.1016/j.carbpol.2015.02.008
C. Tezara, J. P. Siregar, H. Y. Lim, F. A. Fauzi, M. H. Yazdi, L. K. Moey, and J. W. Lim, “Factors that affect the mechanical properties of kenaf fiber reinforced polymer: a review,” Journal of Mechanical Engineering Science, vol. 10, pp. 2159-2175, 2016.
D. Bishnoi, G. P. Singh, and M. S. Shekhawat, “The effect of mercerization on the physical, mechanical, morphological, and chemical properties of aerva tomentosa fiber and fiber-reinforced urea-formaldehyde composites,” Materials Today: Proceedings, article in press, 2023.
I. Jordanov, B. Mangovska, and P. F. Tavčer, “Mechanical and structural properties of mercerized cotton yarns, bio-scoured with pectinases,” Tekstil, vol. 59, pp. 439-446, 2010.
N. Lu, R. H. Swan, and I. Ferguson, “Composition, structure, and mechanical properties of hemp fiber reinforced composite with recycled high-density polyethylene matrix,” Journal of Composite Materials, vol. 46, pp. 1915-1924, 2011. DOI: https://doi.org/10.1177/0021998311427778
J. Correia, F. R. Oliveira, R. C. S. C. Valle, and J. A. B. Valle, “Preparation of cationic cotton through reaction with different polyelectrolytes,” Cellulose, vol. 28, pp. 11679-11700, 2021. DOI: https://doi.org/10.1007/s10570-021-04260-4
J. Correia, K. Mathur, M. Bourham, F. R. Oliveira, R. D. S. C. Valle, J. A. B. Valle, and A. M. Seyam, “Surface functionalization of greige cotton knitted fabric through plasma and cationization for dyeing with reactive and acid dyes,” Cellulose, vol. 28, pp. 9971-9990, 2021. DOI: https://doi.org/10.1007/s10570-021-04143-8
T. Zhang, S. Zhang, W. Qian, J. He, and X. Dong, “Reactive dyeing of cationized cotton fabric: the effect of cationization level,” ACS Sustainable Chemistry & Engineering, vol. 9, pp. 12355-12364, 2021. DOI: https://doi.org/10.1021/acssuschemeng.1c04340
R. Aguado, Q. Tarr´es, P. Mutj´, M. A. P`elach, M. Delgado-Aguilar, “Non-covalently cationized nanocellulose from hemp: kinetics, key properties, and paper strengthening,” Industrial Crops and Products, vol. 188, p. 115582, 2022. DOI: https://doi.org/10.1016/j.indcrop.2022.115582
C. Sampl, J. Schaubeder, U. Hirn, and S. Spirk, “Interplay of electrolyte concentration and molecular weight of polydadmac on cellulose surface adsorption,” International Journal of Biological Macromolecules, vol. 239, p. 124286, 2023. DOI: https://doi.org/10.1016/j.ijbiomac.2023.124286
I. W. Mwangi, J. C. Ngila, P. Ndungu, and T. Msagati, “Preconcentration and spectrophotometric determination of polydadmac in treated water by in situ co-precipitation with naphthalene,” Physics and Chemistry of the Earth, vol. 72-75, pp. 54-60, 2014. DOI: https://doi.org/10.1016/j.pce.2014.07.001
H. Ma, Y. Li, Y. Shen, L. Xie, and D. Wang, “Effect of linear density and yarn structure on the mechanical properties of ramie fiber yarn reinforced composites,” Composites Part A: Applied Science and Manufacturing, vol. 87, pp. 98-108, 2016. DOI: https://doi.org/10.1016/j.compositesa.2016.04.012
T. B. Elmaaty, E. A. El-Aziz, J. Ma, F. El-Taweel, and S. Okubayashi, “Eco-friendly disperse dyeing and functional finishing of nylon 6 using supercritical carbon dioxide,” Fibers, vol. 3, pp. 309-322, 2015. DOI: https://doi.org/10.3390/fib3030309
P. Lyu, L. Xia, X. Jiang, X. Liu, W. Xu, C. Hurren, and X. Wang, “Efficient extraction of technical fibers from hemp in an ethanol-water mixture,” Industrial Crops and Products, vol. 178, p. 114620, 2022. DOI: https://doi.org/10.1016/j.indcrop.2022.114620
D. Dai, and M. Fan, “Characteristic and performance of elementary hemp fibre,” Materials Sciences and Applications, vol. 1, pp. 336-342, 2010. DOI: https://doi.org/10.4236/msa.2010.16049
M. N. Islam, Apparel Fibers. Dhaka: Popular Color & Printing, 2006.
G. F. S. Hussain, K. R. K. Iyer, and N. B. Patil, “Influence of mercerization and crosslinking on the dynamic and static moduli of cotton yarns,” Textile Research Journal, vol. 52, pp. 663-665, 1982. DOI: https://doi.org/10.1177/004051758205201009
Y. A. Sona, J. P. Honga, and T. K. Kim, “An approach to the dyeing of polyester fiber using indigo and its extended wash fastness properties,” Dyes and Pigments, vol. 61, pp. 263-272, 2004. DOI: https://doi.org/10.1016/j.dyepig.2003.11.001
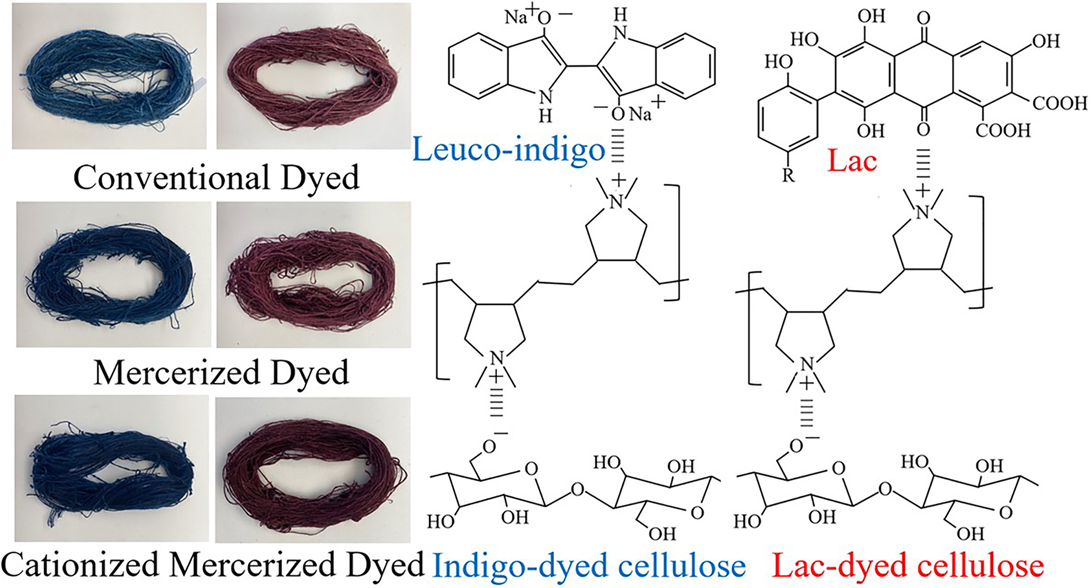
ดาวน์โหลด
เผยแพร่แล้ว
วิธีการอ้างอิง
ฉบับ
บท
การอนุญาต
ลิขสิทธิ์ (c) 2024 วารสารโลหะ, วัสดุ และแร่

This work is licensed under a Creative Commons Attribution-NonCommercial-NoDerivatives 4.0 International License.
Authors who publish in this journal agree to the following terms:
- Authors retain copyright and grant the journal right of first publication with the work simultaneously licensed under a Creative Commons Attribution License that allows others to share the work with an acknowledgment of the work's authorship and initial publication in this journal.
- Authors are able to enter into separate, additional contractual arrangements for the non-exclusive distribution of the journal's published version of the work (e.g., post it to an institutional repository or publish it in a book), with an acknowledgment of its initial publication in this journal.