Development of forming limit diagrams for motorcycle fuel tank made from AA5754-O under deep drawing
DOI:
https://doi.org/10.55713/jmmm.v34i3.2013คำสำคัญ:
Forming limit curve, Laser marking combined with elastic paints, Keeler-Brazier modified Iบทคัดย่อ
The research studied forming limit curves (FLC) for aluminum alloy 5754-O (AA5754-O) and modified them using two methods. These methods aimed to create FLCs for application in describing the forming behavior of sheet metal material through a deep drawing process simulation in the PAM-STAMP program. The methods are as follows: The Nakajima test combined with a new method, a novel process for grid creation on the specimen: laser marking combined with elastic paints. A mathematical material model using the fracture model along with the yield criteria: YLD2000-2D and hardening law: Swift-Voce. The Keeler-Brazier modified equation was chosen as the fracture model for this research because it is an effective equation for creating FLCs for steel materials and has not yet been applied to aluminum materials. Furthermore, no one has previously used the Keeler-Brazier modified equation in conjunction with YLD2000-2D and the yield criterion Swift-Voce hardening law. In summary, the FLC generated from YLD2000-2D, Swift-Voce hardening law, and Keeler-Brazier modified equations can predict the location of damage occurrence on the motorcycle fuel tank, which occurs due to the deep drawing process, using finite element simulation accurately. This closely resembles the actual forming process in the industry.
Downloads
เอกสารอ้างอิง
S. Das, A. Engineering, and C. Analyst, “Design and weight optimization of aluminium alloy wheel,” International Journal of Scientific and Research Publications, vol. 4, no. 6, 2014.
C. Author, “ORIGINAL ARTICLES Magnesium and Aluminum Alloys in Automotive Industry,” 2012. [Online]. Available: http://www.worldaluminium.org.
M. Fadzli Abdollah, and R. Hassan, “Preliminary design of side door impact beam for passenger cars using aluminium alloy”, Journal of Mechanical Engineering and Technology, vol. 5, no. 1, 2010.
B. Ma, C. Yang, X. Wu, and L. Zhan, “Theoretical and numerical investigation of the limit strain of a 5754-O aluminum alloy sheet considering the influence of the hardening law,” Journal Materials Engineering and Performance, vol. 32, pp. 10115-10127, 2023. DOI: https://doi.org/10.1007/s11665-023-07849-x
Q. Hu, and J. W. Yoon, “The roles of yield function and plastic potential under non-associated flow rule for formability prediction with perturbation approach,” in IOP Conference Series: Materials Science and Engineering, IOP Publishing Ltd, 2020. DOI: https://doi.org/10.1088/1757-899X/967/1/012027
M. Türköz, Ö. N. Cora, H. Gedikli, M. Dilmeç, H. S. Halkacı, and M. Koç, “Numerical optimization of warm hydromechanical deep drawing process parameters and its experimental verification,” Journal of Manufacturing Processes, vol. 57, pp. 344-353, 2020. DOI: https://doi.org/10.1016/j.jmapro.2020.06.020
M. Tinkir, M. Dilmeç, M. Türköz, and H. S. Halkaci, “Investigation of the effect of hydromechanical deep drawing process parameters on formability of AA5754 sheets metals by using neuro-fuzzy forecasting approach,” Journal of Intelligent & Fuzzy Systems, vol. 28, pp. 647-659, 2015. DOI: https://doi.org/10.3233/IFS-141346
W. Yuan, M. Wan, and X. Wu, “Prediction of forming limit curves for 2021 aluminum alloy,” in Procedia Engineering, Elsevier Ltd, 2017, pp. 544-549. DOI: https://doi.org/10.1016/j.proeng.2017.10.1018
T. K. Hoang, T. T. Luyen, and D. T. Nguyen, “Enhancing/ improving forming limit curve and fracture height predictions in the single-point incremental forming of Al1050 sheet material,” Materials, vol. 16, no. 23, 2023. DOI: https://doi.org/10.3390/ma16237266
R. Zhang, Z. Shao, and J. Lin, “A review on modelling techniques for formability prediction of sheet metal forming,” International Journal of Lightweight Materials and Manufacture, vol. 1, no. 3, pp. 115-125, 2018. DOI: https://doi.org/10.1016/j.ijlmm.2018.06.003
X. Zhan, Z. Wang, M. Li, Q. Hu, and J. Chen, “Investigations on failure-to-fracture mechanism and prediction of forming limit for aluminum alloy incremental forming process,” Journal of Materials Processing Technology, vol. 282, 2020. DOI: https://doi.org/10.1016/j.jmatprotec.2020.116687
Y. Dewang, M. S. Hora, and S. K. Panthi, “Prediction of crack location and propagation in stretch flanging process of aluminum alloy AA-5052 sheet using FEM simulation,” Transactions of Nonferrous Metals Society of China (English Edition), vol. 25, no. 7, pp. 2308-2320, 2015. DOI: https://doi.org/10.1016/S1003-6326(15)63846-8
“ISO 12004-2 Metallic materials – Sheet and strip – Determination of forming-limit curves. Part 2: Determination of forming- limit curves in the laboratory,” in ISO 12004–2, 2008.
M. Tomáš, E. Evin, S. Németh, and J. Hudák, “Evaluation of limit deformations of zn coated high strength steel,” in Materials Science Forum, vol. 818, pp. 248-251, 2015. DOI: https://doi.org/10.4028/www.scientific.net/MSF.818.248
V. A. M. Cristino, M. B. Silva, P. K. Wong, and P. A. F. Martins, “Determining the fracture forming limits in sheet metal forming: A technical note,” Journal of Strain Analysis for Engineering Design, vol. 52, no. 8, pp. 467-471, 2017. DOI: https://doi.org/10.1177/0309324717727443
K. Mäntyjärvi, J. Tulonen, T. Saarnivuo, J. Porter, and J. A. Karjalainen, “Grid patterns by laser for forming strain analysis,” International Journal of Material Forming, vol. 1, no. 1, pp. 249-252, 2008.
X. Li, Y. Chen, L. Lang, and R. Xiao, “A modified m-k method for accurate prediction of flc of aluminum alloy,” Metals (Basel), vol. 11, no. 3, pp. 1-12, 2021. DOI: https://doi.org/10.3390/met11030394
Z. Q. Sheng, and P. K. Mallick, “Predicting sheet forming limit of aluminum alloys for cold and warm forming by developing a ductile failure criterion,” in Journal of Manufacturing Science and Engineering, Transactions of the ASME, American Society of Mechanical Engineers (ASME), 2017. DOI: https://doi.org/10.1115/MSEC2017-2956
P. Larpprasoetkun, J. Leelaseat, A. Nakwattanaset, A. Sunanta, and S. Suranuntchai, “Study on the material models of the forming limit curves development for predicting a fracture behavior of AA5754-O in automotive parts,” Key Engineering Materials, vol. 973, pp. 81-86, 2024. DOI: https://doi.org/10.4028/p-qme3I9
S. Panich, F. Barlat, V. Uthaisangsuk, S. Suranuntchai, and S. Jirathearanat, “Experimental and theoretical formability analysis using strain and stress based forming limit diagram for advanced high strength steels,” Materials and Design, vol. 51, pp. 756-766, 2013. DOI: https://doi.org/10.1016/j.matdes.2013.04.080
A. L. Gurson, “Continuum theory of ductile rupture by void nucleation and growth: Part 1-Yield criteria and flow rules for porous ductile media,” 1977. [Online]. Available: http://asme.org/terms DOI: https://doi.org/10.1115/1.3443401
S. K. Paul, “Controlling factors of forming limit curve: A review,” Advances in Industrial and Manufacturing Engineering, vol. 2. Elsevier B.V., May 01, 2021. DOI: https://doi.org/10.1016/j.aime.2021.100033
S. K. Paul, “Path independent limiting criteria in sheet metal forming,” Journal of Manufacturing Processes, vol. 20, pp. 291-303, 2015. DOI: https://doi.org/10.1016/j.jmapro.2015.06.025
S. Panich, S. Suranuntchai, S. Jirathearanat, and V. Uthaisangsuk, “A hybrid method for prediction of damage initiation and fracture and its application to forming limit analysis of advanced high strength steel sheet,” Engineering Fracture Mechanics, vol. 166, pp. 97-127, 2016. DOI: https://doi.org/10.1016/j.engfracmech.2016.08.025
A. Nakwattanaset, S. Panich, and S. Suranuntchai, “Formability prediction of high-strength steel sheet using experimental, analytical and theoretical analysis based on strain and stress forming limit curves and its application to automotive forming parts: Vorhersage der Umformbarkeit von hochfesten Stahlblechen mittels experimenteller, analytischer und theoretischer Analyse auf der Grundlage von Grenzformänderungskurven für Dehnungen und Spannungen und ihre Anwendung auf die Umformung von Automobilteilen,” Materwiss Werksttech, vol. 54, no. 9, pp. 1122-1137, 2023. DOI: https://doi.org/10.1002/mawe.202200323
R. Hill, “A theory of the yielding and plastic flow of anisotropic metals,” 1948.
J. Lian, F. Barlat, and B. Baudelet, “Plastic behaviour and stretchability of sheet metals. part II: Effect of yield surface shape on sheet forming limit,” International Journal of Plasticity, vol 5, no. 2, pp. 131-147, 1989. DOI: https://doi.org/10.1016/0749-6419(89)90026-0
D. Banabic, T. Balan, and D. S. Comsa, “A new yield criterion for orthotropic sheet metals under plane-stress conditions.” International Journal of Mechanical Sciences, vol. 45, no. 5, pp. 797-811, 2003. DOI: https://doi.org/10.1016/S0020-7403(03)00139-5
C. C. Roth, and D. Mohr, “Effect of strain rate on ductile fracture initiation in advanced high strength steel sheets: Experiments and modeling,” International Journal of Plasticity, vol. 56, pp. 19-44, 2014. DOI: https://doi.org/10.1016/j.ijplas.2014.01.003
I. Jang, G. Bae, J. Song, H. Kim, and N. Park, “Fracture envelopes on the 3D-DIC and hybrid inverse methods considering loading history,” Materials & Design, vol. 194, p. 108934, 2020. DOI: https://doi.org/10.1016/j.matdes.2020.108934
K. S. Pandya, C. C. Roth, and D. Mohr, “Strain rate and temperature dependent plastic response of AA7075 during hot forming,” in IOP Conference Series Materials Science and Engineering, vol. 651, no. 1, p. 012100, 2019. DOI: https://doi.org/10.1088/1757-899X/651/1/012100
H. Shang, C. Zhang, S. Wang, and Y. Lou, “Large strain flow curve characterization considering strain rate and thermal effect for 5182-O aluminum alloy,” International Journal of Material Forming, vol. 16, no. 1, 2023. DOI: https://doi.org/10.1007/s12289-022-01721-4
ASTM E8, “Standard Test Methods for Tension Testing of Metallic Materials,” in American Association State Highway and Transportation Officials Standard, 2016.
S. Fang, X. Zheng, G. Zheng, B. Zhang, B. Guo, and L. Yang, “A new and direct r-value measurement method of sheet metal based on multi-camera dic system,” Metals (Basel), vol. 11, no. 9, 2021. DOI: https://doi.org/10.3390/met11091401
M. Ghosh, A. Miroux, and L. A. I. Kestens, “Correlating r-value and through thickness texture in Al-Mg-Si alloy sheets,” Journal of Alloys and Compounds, vol. 619, pp. 585-591, 2015. DOI: https://doi.org/10.1016/j.jallcom.2014.09.038
K. Mäntyjärvi, J. Tulonen, T. Saarnivuo, J. Porter, and J. A. Karjalainen, “Grid patterns by laser for forming strain analysis,” International Journal of Material Forming, vol. 1, no. 1, pp. 249-252, 2008. DOI: https://doi.org/10.1007/s12289-008-0355-y
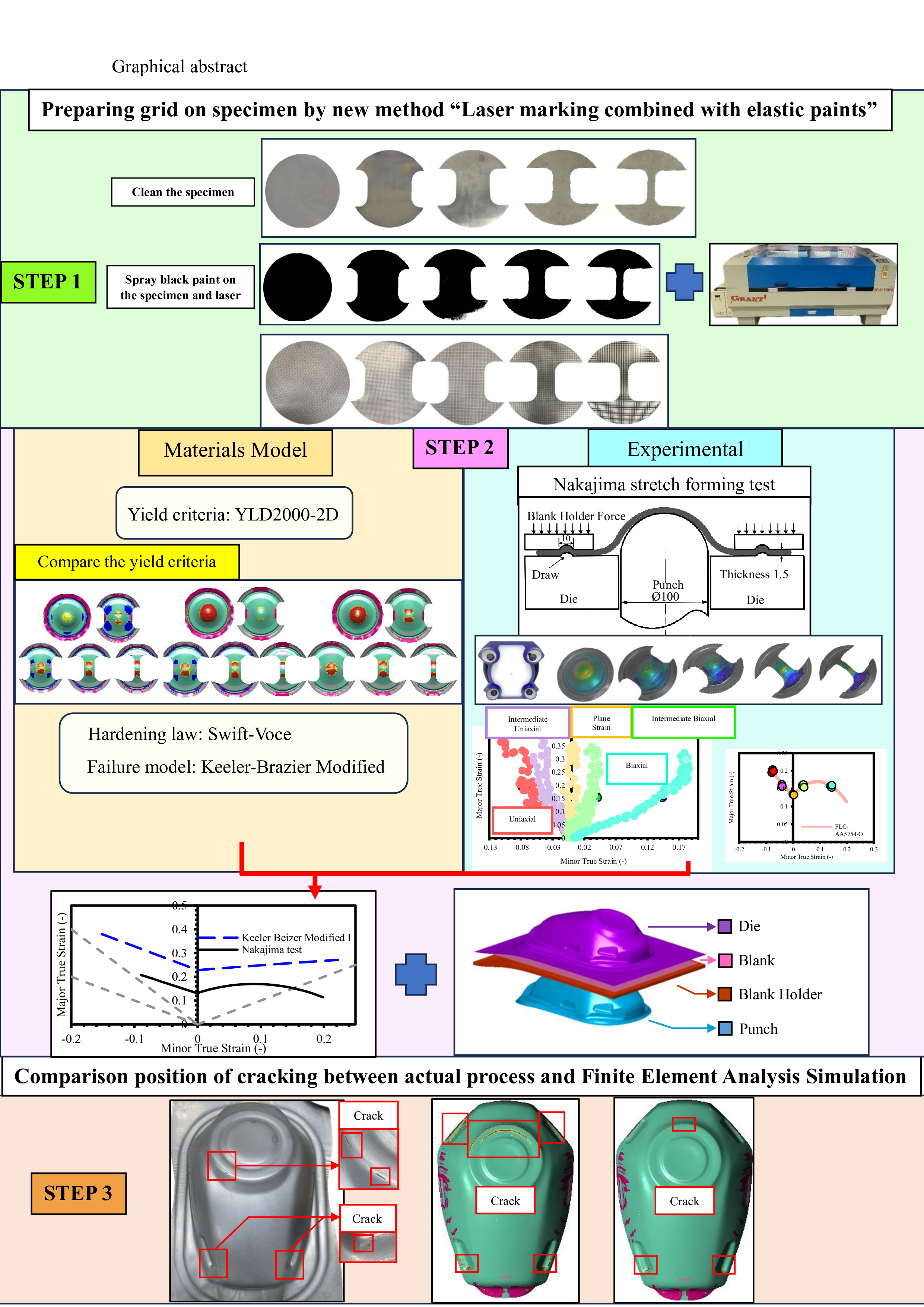
ดาวน์โหลด
เผยแพร่แล้ว
วิธีการอ้างอิง
การอนุญาต
ลิขสิทธิ์ (c) 2024 วารสารโลหะ, วัสดุ และแร่

This work is licensed under a Creative Commons Attribution-NonCommercial-NoDerivatives 4.0 International License.
Authors who publish in this journal agree to the following terms:
- Authors retain copyright and grant the journal right of first publication with the work simultaneously licensed under a Creative Commons Attribution License that allows others to share the work with an acknowledgment of the work's authorship and initial publication in this journal.
- Authors are able to enter into separate, additional contractual arrangements for the non-exclusive distribution of the journal's published version of the work (e.g., post it to an institutional repository or publish it in a book), with an acknowledgment of its initial publication in this journal.