Extraction of molybdenum from a spent HDS catalyst using alkali leaching reagent
DOI:
https://doi.org/10.55713/jmmm.v32i2.1252Keywords:
recycling of metal, molybdenum, spent HDS catalyst, alkaline leaching, metal extractionAbstract
This research investigated extraction of molybdenum from spent hydrodesulfurization (HDS) catalyst used in petroleum refinery. The spent HDS catalyst still however contains significant amounts of valuable metals such as molybdenum and nickel for example, thereby recovery of such metals are of great interest. Pyro-hydrometallurgical process was utilized in this research to selectively extract molybdenum from the spent HDS catalyst using alkali leaching reagent. The process start from calcination of spent HDS catalyst, alkali leaching using sodium carbonate, purification by carbon adsorption-desorption, precipitation of ammonium molybdate and finally calcination to give molybdenum trioxide (MoO3) as the final recycling product. Effects of calcination temperature (450℃ to 650℃) together with alkali concentration (1 M to 3 M Na2CO3), solid to liquid ratio (100 g×L-1 to 300 g×L-1) and leaching time (30 min to180 min) have been investigated. Calcination at 450℃ has shown to give the highest leaching efficiency. The optimum leaching condition, giving 97% leaching efficiency was determined to be 40 g×L-1 sodium carbonate concentration, 2 h-leaching time, 100 g×L-1 solid to liquid ratio and 90℃ leaching temperature, by controlling the temperature at 90℃ and the pH at 2, ammonium molybdate then precipitated. Calcination at 450℃ finally converted the obtained precipitate to molybdenum trioxide as the final recycling product of 99.5% purity.
Downloads
References
R. V. Mom, J. N. Louwen, J. W. M. Frenken, and I. M. N. Groot, “In situ observations of an active MoS2 model hydrodesulfurization catalyst,” Nature Communications, vol. 10, 2546, 2019. DOI: https://doi.org/10.1038/s41467-019-10526-0
S. Huang, J. Liu, C. Zhang, B. Hu, X. Wang, M. Wang, and X. Wang, “Extraction of molybdenum from spent HDS catalyst by two-stage roasting followed by water leaching,” Journal of Metals, vol. 71, no. 12, pp. 4681-4686, 2019. DOI: https://doi.org/10.1007/s11837-019-03741-z
S. Helveg, J. V. Lauritsen, E. Lægsgaard, I. Stensgaard, J. K. Nørskov, B. S. Clausen, H. Topsøe, and F. Besenbacher, “Atomic-scale structure of single-layer mos2 nanoclusters,” Physical Review Letters, vol. 84, no. 5, pp. 951-954, 2000. DOI: https://doi.org/10.1103/PhysRevLett.84.951
S. S. Bello, C. Wang, M. Zhang, H. Gao, Z. Han, L. Shi, F. Su, and G. Xu, “A review on the reaction mechanism of hydro-desulfurization and hydrodenitrogenation in heavy oil upgrading,” Energy & Fuels, vol. 35, no. 14, pp. 10998-11016, 2021. DOI: https://doi.org/10.1021/acs.energyfuels.1c01015
M. Marafi, and A. Stanislaus, “Spent catalyst waste management: A review – Part I- Development in hydroprocessing catalyst waste reduction and use,” Resource, Conservation and Recycling, vol. 52, no. 6, pp. 859-873, 2008. DOI: https://doi.org/10.1016/j.resconrec.2008.02.004
A. Yaraş, and H. Arslanoğlu, “Extraction of selected metals from spent hydrodesulfurization catalyst using alkali leaching agent,” Separation Science and Technology, vol. 55, no. 11, pp. 1-12, 2020. DOI: https://doi.org/10.1080/01496395.2019.1673412
L. Zeng, and C. Y. Cheng, “A literature review of the recovery of molybdenum and vanadium from spent hydrodesulphurisation catalysts. Part I: Metallurgical processes,” Hydrometallurgy, vol. 98, no. 1-2, pp. 1-9, 2009. DOI: https://doi.org/10.1016/j.hydromet.2009.03.010
L. Zeng, and C. Y. Cheng, “A literature review of the recovery of molybdenum and vanadium from spent hydrodesulphurisation catalysts: Part II Separation and purification,” Hydrometallurgy, vol. 98, no. 1-2, pp. 10-20, 2009. DOI: https://doi.org/10.1016/j.hydromet.2009.03.012
M. Marafi, M. S. Rana, R. Navvamani, and H. Al-Sheeha, “Utilization of waste spent hydroprocessing catalyst: development of a process for full recovery of deposited metals and alumina support,” Waste Management and the Environment VI, WIT Transactions on Ecology and The Environment, WIT Press, vol. 163, pp. 237-249, 2012 DOI: https://doi.org/10.2495/WM120221
I. Asghari, S. M. Mousavi, F. Amiri, and S. Tavassoli, “Bioleaching of spent refinery catalysts: A review,” Journal of Industrial and Engineering Chemistry, vol. 19, no. 4, pp. 1069-1081, 2013. DOI: https://doi.org/10.1016/j.jiec.2012.12.005
S. Ilhan, “Leaching of spent Ni-Mo hydrodesulphurization (HDS) catalyst in oxalic acid solutions,” The Minerals, Metals & Materials Series, Proceedings of the 3rd Pan American Materials Congress, pp. 557-564, 2017. DOI: https://doi.org/10.1007/978-3-319-52132-9_56
B. B. Kar, P. Datta, and V. N. Misra, “Spent catalyst: secondary source for molybdenum recovery,” Hydrometallurgy, vol. 72, no. 1-2, pp. 87-92, 2004. DOI: https://doi.org/10.1016/S0304-386X(03)00122-1
K. H. Park, D. Mohapatra, and B. R. Reddy, “Selective recovery of molybdenum from spent HDS catalyst using oxidative soda ash leach/carbon absorption method,” Journal of Hazardous Materials, vol. 138, no. 2, pp. 311-316, 2006. DOI: https://doi.org/10.1016/j.jhazmat.2006.05.115
J-M. Yoo, J-C. Lee, B-S Kim, H. S. Lee, and J-K Jeong, “Leaching of nickel from a hydrodesulphurization spent catalyst with ammonium sulfate,” Journal of Chemical Engineering of Japan, vol. 37, no. 9, pp. 1129-1134, 2004. DOI: https://doi.org/10.1252/jcej.37.1129
G. L. Tilley, and C. M. Calif, “Recovery of metal values from spent catalysts,” United State Patent, no. 4,721,606, Jan. 26, 1988.
E. I. Wiewiorowski, L. R. Tinnin, and R. Crnojevich, “A cyclic process for recovery of metals from spent catalysts,” United State Patent, no. 4,670,229, Jan. 2, 1987.
D. Mohapatra, and K. H. Park, “Selective recovery of Mo, Co and Al from spent Co/Mo/γ -Al2O3 catalyst: Effect of calcination temperature,” Journal of Environmental Science and Health, Part A, vol. 42, no. 4, pp. 507-515, 2007. DOI: https://doi.org/10.1080/10934520601188409
A. S. Medvedev, and N. V. Malochkina, “Sublimation of molybdenum trioxide from exhausted catalysts employed for the purification of oil products,” Russian Journal of Non-Ferrous Metals, vol. 48, no. 2, pp. 114-117, 2007. DOI: https://doi.org/10.3103/S1067821207020071
S. Sadighi, and S. K. M. Targhi, “Precipitation of biofuel from palm oil catalysis by ammonium molybdate in homogeneous,” Bulletin of Chemical Reaction Engineering & Catalyst, vol. 12, no. 1, pp. 49-54, 2016. DOI: https://doi.org/10.9767/bcrec.12.1.486.49-54
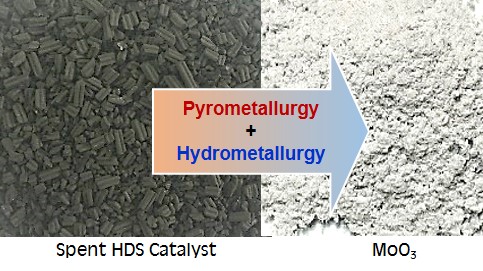
Downloads
Published
How to Cite
Issue
Section
License
Copyright (c) 2022 Journal of Metals, Materials and Minerals

This work is licensed under a Creative Commons Attribution-NonCommercial-NoDerivatives 4.0 International License.
Authors who publish in this journal agree to the following terms:
- Authors retain copyright and grant the journal right of first publication with the work simultaneously licensed under a Creative Commons Attribution License that allows others to share the work with an acknowledgment of the work's authorship and initial publication in this journal.
- Authors are able to enter into separate, additional contractual arrangements for the non-exclusive distribution of the journal's published version of the work (e.g., post it to an institutional repository or publish it in a book), with an acknowledgment of its initial publication in this journal.