Ballistic performance of composite armor impacted by 7.62 mm armor projectile
DOI:
https://doi.org/10.55713/jmmm.v33i2.1698Keywords:
alumina ceramic, aluminum cubic lattice sandwich panels, armor, ballistic performanceAbstract
The purpose of this study is to investigate the effectiveness of composite armor against 7.62 mm ballistic threats. A sandwich panel construction consisting of a 96% alumina ceramic strike face, an annealed aluminum alloy 7075 cubic lattice sandwich panel, and a thin aluminum backing plate were used to create hard armor. The ballistic test based on NIJ standard level III was performed using 7.62 mm × 51 mm NATO projectiles at an impact velocity of 847 ± 9.1 m∙s-1. The influences of the alumina strike face panel with thicknesses of 7, 10, and 14 mm on the ballistic performance were investigated. The results of the ballistic test suggest that hard armor designs can resist a ballistic impact of 7.62 mm × 51 mm NATO projectiles without penetrating them. With the increase in thickness of alumina ceramic tile, the deformation of the aluminum backing plate decreased. Furthermore, the annealed aluminum alloy 7075 cubic lattice sandwich panel could be able to absorb the residual kinetic energy of the projectile after it was eroded by the ceramic strike panel. The damaged targets after ballistic impact were presented. Collectively, these results indicate that the armor composites in this study may be used in military vehicle applications.
Downloads
References
E. Medvedovski, “Ballistic performance of armour ceramics: Influence of design and structure. Part 1,” Ceramics International, vol. 36, no. 7, pp. 2103-2115, 2010.
K. Dateraksa, K. Sujirote, R. McCUISTON, and D. Atong, “Ballistic performance of ceramic/S2-glass composite armor,” Journal of Metals, Materials and Minerals, vol. 22, no. 2, pp. 33-39, 2012.
M. V. Silva, D. Stainer, H. A. Al-Qureshi, O. R. K. Montedo, and D. Hotza, “Alumina-based ceramics for armor application: mechanical characterization and ballistic testing,” Journal of Ceramics, 2014.
W. Liu, Z. Chen, X. Cheng, Y. Wang, A. R. Amankwa, and J. Xu, “Design and ballistic penetration of the ceramic composite armor,” Composites Part B: Engineering, vol. 84, pp. 33-40, 2016.
D. Hu, Y. Zhang, Z. Shen, and Q. Cai, “Investigation on the ballistic behavior of mosaic SiC/UHMWPE composite armor systems,” Ceramics International, vol. 43, no. 13, pp. 10368-10376, 2017.
I. G. Crouch, G. Appleby-Thomas, and P. J. Hazell, “A study of the penetration behaviour of mild-steel-cored ammunition against boron carbide ceramic armours,” International Journal of Impact Engineering, vol. 80, pp. 203-211, 2015.
Z. Yin, J. Yuan, M. Chen, D. Si, and C. Xu, “Mechanical property and ballistic resistance of graphene platelets/B4C ceramic armor prepared by spark plasma sintering,” Ceramics International, vol. 45, no. 17, pp. 23781-23787, 2019.
L. Peroni, M. Avalle, and M. Peroni, “The mechanical behaviour of aluminium foam structures in different loading conditions,” International Journal of Impact Engineering, vol. 35, no. 7, pp. 644-658, 2008.
B. A. Gama, J. W. Gillespie, T. A. Bogetti, and B. K. Fink, “Innovative design and ballistic performance of lightweight composite integral armor,” SAE transactions, vol. 110, no. 2, pp. 32-41, 2001.
B. A. Gama, T. A. Bogetti, B. K. Fink, C. J. Yu, T. D. Claar, H. H. Eifert, and J. W. Gillespie Jr, “Aluminum foam integral armor: a new dimension in armor design,” Composite Structures, vol. 52, pp. 381-385, 2001.
J. Banhart, F. García-Moreno, K. Heim, and H. W. Seeliger, “Light-weighting in transportation and defence using aluminium foam sandwich structures,” In Light Weighting for Defense, Aerospace, and Transportation, pp. 61-72, 2019.
A. Rabiei, L. Vendra, N. Reese, N. Young, and B. P. Neville, “Processing and characterization of a new composite metal foam,” Materials Transactions, vol. 47, no. 9, pp. 2148-2153, 2006.
B. P. Neville, and A. Rabiei, “Composite metal foams processed through powder metallurgy,” Materials & Design, vol. 29, no. 2, pp. 388-396, 2008.
M. Garcia-Avila, M. Portanova, and A. Rabiei, “Ballistic performance of a composite metal foam-ceramic armor system,” Procedia Materials Science, vol. 4, pp. 151-156, 2014.
J. Marx, M. Portanova, and A. Rabiei, “Ballistic performance of composite metal foam against large caliber threats,” Composite Structures, vol. 225, p. 111032, 2019.
O. Al-Ketan, R. K. A. Al-Rub, and R. Rowshan, “The effect of architecture on the mechanical properties of cellular structures based on the IWP minimal surface,” Journal of Materials Research, vol. 33, no. 3, pp. 343-359, 2018.
A. Bhat, “Honeycomb in hybrid composite armor resisting dynamic impact,” Doctoral dissertation, Oklahoma State University, 2015.
A. du Plessis, and C. Broeckhoven, “Metal body Armour: biomimetic engineering of lattice structures,” 19th Annual International RAPDASA conference, 2018.
D. Hu, Y. Zhang, Z. Shen, and Q. Cai, “Investigation on the ballistic behavior of mosaic SiC/UHMWPE composite armor systems,” Ceramics International, vol. 43, no. 13, pp. 10368-10376, 2017.
H. Y. Sarvestani, A. H. Akbarzadeh, A. Mirbolghasemi, and K. Hermenean, “3D printed meta-sandwich structures: Failure mechanism, energy absorption and multi-hit capability,” Materials & Design, vol. 160, pp. 179-193, 2018.
G. H. Liaghat, H. Shanazari, M. Tahmasebi, A. Aboutorabi, and H. Hadavinia, “A modified analytical model for analysis of perforation of projectile into ceramic composite targets,” Journal of Composite Materials, vol. 3, pp. 17-22, 2013.
K. Sujirote, K. Dateraksa, and N. Chollacoop, “Practical requirements for alumina armor systems,” American Ceramic Society Bulletin, vol. 86, no. 3, pp. 20-25, 2007.
F. De Oliveira Braga, F. S. da Luz, S. N. Monteiro, and É. P. Lima Jr, “Effect of the impact geometry in the ballistic trauma absorption of a ceramic multilayered armor system,” Journal of Materials Research and Technology, vol. 7, no. 4, pp. 554-560, 2018.
A. D. Isadare, B. Aremo, M. O. Adeoye, O. J. Olawale, and M. D. Shittu, “Effect of heat treatment on some mechanical properties of 7075 aluminium alloy,” Materials Research, vol. 16, pp. 190-194, 2013.
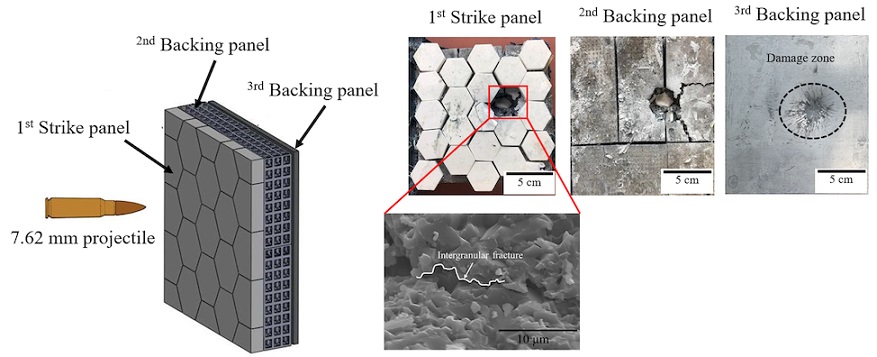
Downloads
Published
How to Cite
Issue
Section
License
Copyright (c) 2023 Journal of Metals, Materials and Minerals

This work is licensed under a Creative Commons Attribution-NonCommercial-NoDerivatives 4.0 International License.
Authors who publish in this journal agree to the following terms:
- Authors retain copyright and grant the journal right of first publication with the work simultaneously licensed under a Creative Commons Attribution License that allows others to share the work with an acknowledgment of the work's authorship and initial publication in this journal.
- Authors are able to enter into separate, additional contractual arrangements for the non-exclusive distribution of the journal's published version of the work (e.g., post it to an institutional repository or publish it in a book), with an acknowledgment of its initial publication in this journal.