Recycling of exhausted dust from regenerator of glass furnace in glass batch melting
DOI:
https://doi.org/10.55713/jmmm.v32i2.1263คำสำคัญ:
Exhausted dust, Regenerator, Glass batch melting, Thermal propertiesบทคัดย่อ
In soda-lime glass manufacturing, evaporation of volatile compounds from glass melt is the origin of the dust emission from glass tank furnace. The exhausted dust then is deposited on the regenerator and is needed to be removed. Thus, this study focuses on using the dust from melting glass in glass production. The glass batches were prepared from 0 wt% to 10 wt% of the exhausted dust from soda-lime glass production as a substitution of the total raw materials. The analysis of phase and chemical composition of the dust by x-ray powder diffraction (XRD) and x-ray fluorescence technique (XRF) indicated that it consisted mainly sodium sulphate. Thermal analysis (TG/DSC) revealed that the addition of exhausted dust reduced the temperature of the melting reaction of the glass batches. The optimum amount of the exhausted dust, which made it possible to obtain the glass with the lowest number of remaining bubbles, was 2 wt%. From CIE lab and dilatometry results revealed that up to 2 wt% replacement of total raw materials by the exhausted dust in the glass batch did not affect the glass color, thermal expansion coefficient, glass transition temperature and dilatometric softening point of glass samples.
Downloads
เอกสารอ้างอิง
J. E. Shelby, Introduction to glass science and technology, 2nd ed. Royal Society of Chemistry, 2005.
H. A. Schaeffer, "Scientific and technological challenges of industrial glass melting," Solid state Ionics, vol. 105, pp. 265-270, 1998. DOI: https://doi.org/10.1016/S0167-2738(97)00478-5
J. Matousek, "Chemistry of evaporation from silicate melts," in The 6th ESG conference; glass odyssey, Montpellier, France. 2002.
R. G. C. Beerkens, "Deposits and condensation from flue gases in glass furnaces," Ph.D., Chemical Engineering and Chemistry, Technische Universiteit Eindhoven, Eindhoven, 1986.
R. G. C. Beerkens, "The role of gases in glass melting," Glass Science and Technology, vol. 71, pp. 369-380, 1995.
H. G. Pfaender, Schott Guide to Glass, 2nd ed. Netherlands: Springer, 1995. DOI: https://doi.org/10.1007/978-94-011-0517-0
V. Sardeshpande, R. Anthony, U.N. Gaitonde, and R. Banerjee, “Performance analysis for glass furnace regenerator,”Applied Energy, vol. 88, pp. 4451-4458, 2011. DOI: https://doi.org/10.1016/j.apenergy.2011.05.028
A. Kasper, E. Carduck, M. Manges, and H. Stadelmann, “Contribution to the characterization of dust emission in glass melting furnaces,” Ceramic Engineering and Science Proceeding, vol. 27, pp. 203-214, 2008. DOI: https://doi.org/10.1002/9780470291306.ch16
N. I. Min’ko, and I. M. binaliev, “Role of sodium sulfate in glass technology,” Glass and Ceramics, vol. 69, pp. 361-365, 2013. DOI: https://doi.org/10.1007/s10717-013-9479-8
J. Mukerji, “Use of sodium sulphate in glass batch part I-Melting accelerator”, Kanch, vol. 3, pp. 15-20, 2010.
H. A. Schaeffer, “Recycling of cullet and filter dust in the German glass industry,” Glass Science and Technol., vol. 69, pp. 101-106, 1996.
Z. Jakubikova, M. Liska, A. Pisko and J. Pagacova, “Study of properties of the glass batch melting filter dust”, Journal of Thermal Analytical Calorimetry, vol. 108, pp. 493-496, 2012. DOI: https://doi.org/10.1007/s10973-011-1961-3
C. R. Bamford, “Colour generation and control in glass,” Elsevier Scientific Publishers, Amsterdam, Netherland, 1977.
P. R. Laimbock, "Foaming of Glass Melts," Ph.D., Technical University of Eindhoven, Eindhoven, Netherlands, 1998.
M. Hujova’, and M. Vernerova,“Influence of fining agents on glass melting: A review, part 1”, Ceramics-Silikáty, vol. 61, pp. 119-126, 2017. DOI: https://doi.org/10.13168/cs.2017.0006
A. Kusnierz, M. Sroda, M. Kosmal, and P. Pichniarczyk, “Thermal analysis of the glass batch with a higher content of raw materials substitution based on selected fining agents,” Journal of Thermal Analytical Calorimetry, vol. 130, pp. 229-247, 2017. DOI: https://doi.org/10.1007/s10973-017-6450-x
M. Hubert, A. Faber, H. Sesigur, and F. Akmaz, "Impact of Redox in Industrial Glass Melting and Importance of Redox Control," in 77th Conference on Glass Problems, Greater Columbus Convention Center, Columbus, OH, vol. 38, no. 1, 2016. DOI: https://doi.org/10.1002/9781119417507.ch11
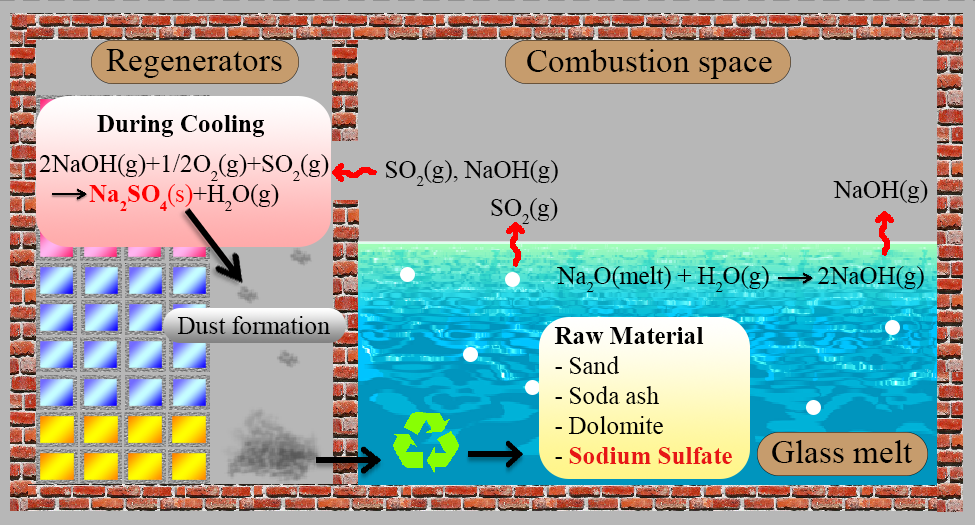
ดาวน์โหลด
เผยแพร่แล้ว
วิธีการอ้างอิง
ฉบับ
บท
การอนุญาต
ลิขสิทธิ์ (c) 2022 Journal of Metals, Materials and Minerals

This work is licensed under a Creative Commons Attribution-NonCommercial-NoDerivatives 4.0 International License.
Authors who publish in this journal agree to the following terms:
- Authors retain copyright and grant the journal right of first publication with the work simultaneously licensed under a Creative Commons Attribution License that allows others to share the work with an acknowledgment of the work's authorship and initial publication in this journal.
- Authors are able to enter into separate, additional contractual arrangements for the non-exclusive distribution of the journal's published version of the work (e.g., post it to an institutional repository or publish it in a book), with an acknowledgment of its initial publication in this journal.