Eddy current evaluation for thickness loss estimation of aluminum alloys used in aircraft structures
DOI:
https://doi.org/10.55713/jmmm.v33i3.1581คำสำคัญ:
NDT, Eddy current evaluation, Corrosion rate, Experiment and analysisบทคัดย่อ
Aluminum alloys are commonly used in the aircraft industry but it tends to corrode and needs to be inspected properly. Eddy current testing is the widely used non-destructive testing (NDT) for aircraft metals. This research studied estimating the thickness loss due to corrosion in an aircraft aluminum sheet metal. The Al1100, Al2024, and Al7075 were 2 mm thick. Aluminum sheet metals were used to create artificial damage in hydrochloric acid. The thickness loss due to corrosion was inspected with eddy current testing (ET) and compared with the measurement from the coordinate measurement machine (CMM). The results showed that the thickness loss due to corrosion could be estimated using the eddy current skin depth frequencies. However, in the practical application, the skin depth could be guessed from the corrosion rate which could reduce the inspection time. In this research, the corrosion rate was measured by using potentiodynamic measurement. It can be used for estimating the thickness loss for an appropriate inspection interval.
Downloads
เอกสารอ้างอิง
J. R. Brence, and D.E. Brown, “Data mining corrosion from eddy current non-destructive tests,” Computer & Industrial Engineering, vol. 43, pp. 821- 840, 2002.
J. Hernandez, Q. Fouliard, K. Vo, and S. Raghavan, “Detection of corrosion under insulation on aerospace structure via pulse eddy current thermography,” Aerospace Science and Technology, vol. 121, p. 107317, 2022.
N. Yusa, and H. Hashizume, “Evaluation of stress corrosion cracking as a function of its resistance to eddy currents,” Nuclear Engineering and Design, vol. 239, pp. 2713-2718, 2009.
N. Yusa, S. Perrin, and K. Miya, “Eddy current data for characterizing less volumetric stress corrosion cracking in nonmagnetic materials,” Materials letters, vol. 61, pp. 827-829, 2007.
N. Yusa, L. Janousek, M. Rebican, Z. Chen, K. Miya, N. Dohi, N. Chiguasa, and Y. Matsumoto, “Caution when applying eddy current inversion to stress corrosion cracking,” Nuclear Engineering and Design, vol. 236, pp. 211-221, 2006.
H. S. Shim, M. S. Choi, D. H. Lee, and D. H. Hur, “A prediction method for the general corrosion behavior of Alloy 690 steam generator tube using eddy current testing,” Nuclear Engineering and Design, vol. 97, pp. 26-31, 2016.
K. Sodsai, M. Noipitak, V. Tangwarodomnukun, and C. Dumkum, “Probe designing for corrosion inspection under insulated surface by using eddy current method,” The Journal of Industrial Technology, vol. 14, no. 2, N. pag. (in Thai), 2018.
H. Shaikh, N. Sivaibharasi, B. Sasi, T. Anita, R. Amirthalingam, B. P. C. Rao, T. Jayakumar, H. S. Khatak, and B. Raj, “Use of eddy current testing method in detection and evaluation of sensitization and intergranular corrosion in austenitic stainless steels,” Corrosion Science, vol. 48, pp. 1462-1482, 2006.
Y. Li, B. Yan, D. Li, Y. Li, and D. Zhou, “Gradient-field pulsed eddy current probes for imaging of hidden corrosion in conductive structures,” Sensors and Actuators, vol. 238, pp. 251-265, 2016.
N. Yusa, Z. Chen, K. Miya, T. Uchimoto, and T. Takagi, “Large-scale parallel computation for the reconstruction of natural stress corrosion cracks from eddy current testing signals,” NDT&E International, vol. 36, pp. 449-459, 2003.
N. Yusa, and K. Miya, “Discussion on the equivalent conductivity and resistance of stress corrosion cracks in eddy current simulations,” NDT&E International, vol. 42, pp. 9-15, 2009.
S. Hosseini, and A. A. Lakis, “Application of time-frequency analysis for automatic hidden corrosion detection in a multilayer aluminum structure using pulsed eddy current,” NDT&E International, vol. 47, pp. 70-79, 2012.
Y. Li, B. Yan, D. Li, Y. Li, and Z. Chen, “Pulse-modulation eddy current inspection of subsurface corrosion in conductive structures,” NDT&E International, vol. 79, pp. 142-149, 2016.
Y. He, G. Y. Tian, M. Pan, D. Chen, and H. Zhang, “An investigation into eddy current pulsed thermography for detection of corrosion blister,” Corrosion Science, vol. 78, pp. 1-6, 2014.
H. M. G. Ramos, O. Postolache, F. C. Alegria, and A. L. Ribeiro, “Using the skin effect to estimate cracks depths in structures,” Instrumentation and Measurement Technology Conference, N. pag, 2009.
ASTM Standard G102-89, “Standard practice for calculation of corrosion rates and related information from electrochemical measurements,” ASTM International, West Conshohocken, PA, 2004.
ASTM Standard G1-03, “Standard Practice for Preparing, Cleaning, and Evaluating Corrosion Test Specimens,” ASTM International, West Conshohocken, PA, 2004.
N. Bowler, Eddy-current nondestructive evaluation, 1st Ed., Springer Science + Business Media, NY, USA, 2019.
C. J. Hellier, Handbook of nondestructive evaluation, 1st Ed., The McGraw-Hill Companies, Inc., USA, 2003.
H. M. Obispo, L. E. Murr, R. M. Arrowood, and E. A. Trillo, “Copper deposition during the corrosion of aluminum alloy 2024 in sodium chloride solution,” Journal of Materials Science, vol. 35, pp. 3479-3495, 2000.
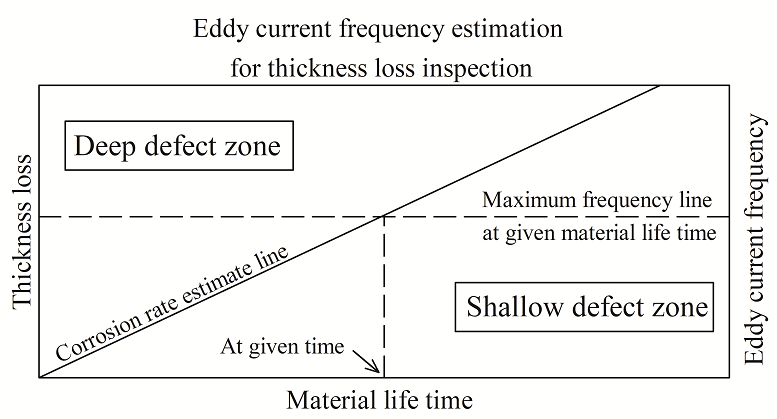
ดาวน์โหลด
เผยแพร่แล้ว
วิธีการอ้างอิง
ฉบับ
บท
การอนุญาต
ลิขสิทธิ์ (c) 2023 วารสารโลหะ, วัสดุ และแร่

This work is licensed under a Creative Commons Attribution-NonCommercial-NoDerivatives 4.0 International License.
Authors who publish in this journal agree to the following terms:
- Authors retain copyright and grant the journal right of first publication with the work simultaneously licensed under a Creative Commons Attribution License that allows others to share the work with an acknowledgment of the work's authorship and initial publication in this journal.
- Authors are able to enter into separate, additional contractual arrangements for the non-exclusive distribution of the journal's published version of the work (e.g., post it to an institutional repository or publish it in a book), with an acknowledgment of its initial publication in this journal.